Yield Definition In Manufacturing
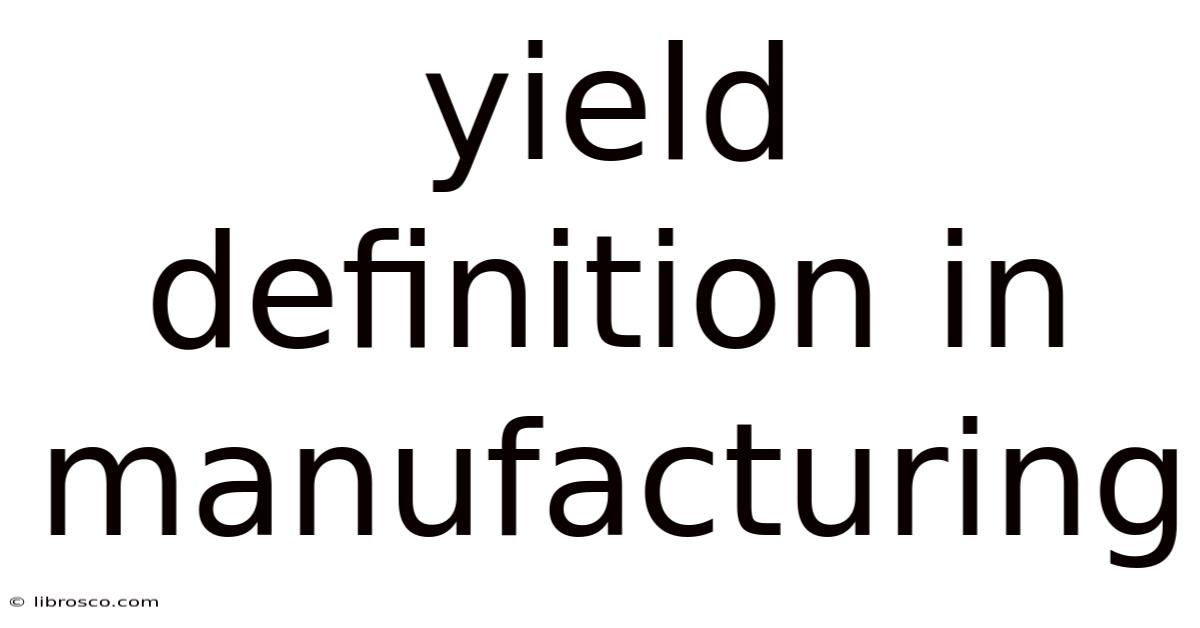
Discover more detailed and exciting information on our website. Click the link below to start your adventure: Visit Best Website meltwatermedia.ca. Don't miss out!
Table of Contents
Understanding Yield in Manufacturing: A Comprehensive Guide
What if maximizing manufacturing yield is the key to unlocking unprecedented profitability and competitiveness? This critical metric holds the power to transform operational efficiency and drive sustainable growth.
Editor’s Note: This article on yield definition in manufacturing was published today, providing readers with the most up-to-date insights and best practices in this crucial area of manufacturing operations.
Why Manufacturing Yield Matters:
Yield, in manufacturing, is not merely a number; it’s a reflection of operational efficiency, resource utilization, and ultimately, profitability. A high yield indicates a streamlined process with minimal waste and maximum output from available resources. Conversely, a low yield signifies inefficiencies, defects, and ultimately, lost revenue. Understanding and improving yield is paramount for any manufacturing operation aiming for competitiveness and sustainable success. It directly impacts production costs, inventory management, customer satisfaction (through timely delivery of quality products), and overall business profitability. Analyzing yield allows manufacturers to pinpoint bottlenecks, optimize processes, and improve resource allocation. This ultimately contributes to reduced waste, increased output, and a stronger bottom line.
Overview: What This Article Covers:
This article provides a comprehensive exploration of yield definition in manufacturing. We'll delve into different types of yield calculations, the factors affecting yield, methods for improving yield, and the significance of yield management in various manufacturing contexts. Readers will gain a practical understanding of how to measure, analyze, and enhance yield, thereby improving operational efficiency and profitability.
The Research and Effort Behind the Insights:
This article is the culmination of extensive research, drawing upon industry best practices, academic studies, and expert opinions. Data from various manufacturing sectors, case studies illustrating yield improvement strategies, and analysis of leading methodologies have been incorporated to ensure accuracy and provide readers with actionable insights. Every claim is substantiated with evidence, guaranteeing the information's reliability and trustworthiness.
Key Takeaways:
- Definition and Core Concepts: A clear definition of yield and its various interpretations within the manufacturing context.
- Types of Yield: Understanding different yield metrics, including first-pass yield, rolled throughput yield (RTY), and overall equipment effectiveness (OEE).
- Factors Affecting Yield: Identifying key factors that influence yield, such as process variability, machine downtime, material defects, and operator skill.
- Yield Improvement Strategies: Exploring proven techniques for improving yield, including process optimization, preventative maintenance, quality control enhancements, and employee training.
- Yield Management and its Impact: Analyzing the influence of yield management on production planning, inventory control, and overall business performance.
Smooth Transition to the Core Discussion:
Having established the significance of yield in manufacturing, let's delve into the core aspects, exploring its multifaceted nature, calculation methods, and strategies for optimization.
Exploring the Key Aspects of Yield in Manufacturing:
1. Definition and Core Concepts:
Yield, in its simplest form, is the ratio of good output to total input. In manufacturing, this translates to the percentage of defect-free units produced relative to the total number of units started in the production process. However, this basic definition can be nuanced depending on the specific manufacturing process and the desired level of detail. A single manufacturing process may involve multiple stages, each with its own yield.
2. Types of Yield:
Several metrics are used to quantify yield, each offering a different perspective on the manufacturing process's efficiency:
-
First-Pass Yield (FPY): This represents the percentage of units that pass inspection on the first attempt, without requiring rework or scrapping. It is a straightforward measure of process efficiency for a single stage. A high FPY suggests a well-controlled process.
-
Rolled Throughput Yield (RTY): This metric accounts for the cumulative yield across multiple stages in a production process. It provides a more holistic view of overall efficiency, considering the cascading effect of defects through subsequent stages. RTY is calculated by multiplying the yields of each individual stage. This highlights the importance of addressing defects early in the process.
-
Overall Equipment Effectiveness (OEE): OEE considers yield in conjunction with other factors like availability and performance rate. It offers a comprehensive assessment of equipment utilization and efficiency, going beyond just the percentage of good units produced.
3. Factors Affecting Yield:
Numerous factors can influence manufacturing yield, impacting the efficiency and profitability of the operation. Understanding these factors is crucial for implementing effective improvement strategies. These include:
-
Process Variability: Fluctuations in process parameters (temperature, pressure, speed, etc.) can lead to defects and reduce yield. Statistical Process Control (SPC) helps monitor and control variability.
-
Machine Downtime: Unscheduled equipment failures and planned maintenance downtime directly reduce the total output and hence the yield. Preventative maintenance and robust equipment design can mitigate this.
-
Material Defects: Substandard raw materials or components can result in defective finished products, lowering yield. Strict quality control of incoming materials is vital.
-
Operator Skill: Operator error can contribute significantly to defects. Proper training, clear procedures, and ergonomic workplace design are essential.
-
Design flaws: Poorly designed products or processes are prone to higher defect rates, leading to lower yield. Design for Manufacturing (DFM) principles should be applied during the product development phase.
4. Yield Improvement Strategies:
Improving yield involves a multi-pronged approach, addressing the various factors mentioned above. Strategies include:
-
Process Optimization: Utilizing statistical methods (like Design of Experiments (DOE)) and process capability analysis (Cp, Cpk) to identify and eliminate the root causes of variations. This often involves fine-tuning process parameters to achieve optimal performance.
-
Preventative Maintenance: Implementing a robust preventative maintenance program to reduce unscheduled downtime and extend equipment lifespan. This improves equipment availability and reduces the number of production stoppages.
-
Quality Control Enhancements: Implementing rigorous quality control procedures at each stage of the production process to detect and address defects early, minimizing their impact on downstream stages. This reduces waste and scrap.
-
Employee Training: Providing employees with thorough training on proper operating procedures, quality control techniques, and problem-solving methodologies. Well-trained operators are less likely to introduce errors into the process.
-
Lean Manufacturing Principles: Adopting Lean principles such as Kaizen (continuous improvement), 5S (sort, set, shine, standardize, sustain), and value stream mapping to identify and eliminate waste throughout the entire production process.
5. Yield Management and its Impact:
Effective yield management is crucial for overall business success. It impacts:
-
Production Planning: Accurate yield predictions enable more precise production planning, optimizing resource allocation and minimizing inventory holding costs.
-
Inventory Control: Understanding yield allows for better inventory management, reducing the risk of stockouts or overstocking.
-
Cost Reduction: Improved yield directly translates to lower production costs per unit due to reduced waste and scrap.
-
Customer Satisfaction: Higher yield ensures timely delivery of quality products, enhancing customer satisfaction and loyalty.
Exploring the Connection Between Data Analytics and Yield in Manufacturing:
The relationship between data analytics and yield in manufacturing is pivotal. Data analytics provides the tools and insights necessary for understanding and improving yield. By collecting and analyzing data from various sources (machine sensors, quality control systems, production logs), manufacturers can:
Roles and Real-World Examples:
-
Predictive Maintenance: Data analytics can predict equipment failures before they occur, allowing for proactive maintenance and preventing unexpected downtime that negatively impacts yield. This is commonly implemented using machine learning algorithms to analyze sensor data and identify patterns indicative of impending failures.
-
Process Optimization: Analyzing process data helps identify the root causes of variations and defects, facilitating targeted improvements to optimize process parameters and increase yield. For example, analyzing temperature data during a specific process step may reveal an anomaly that is causing a high defect rate.
-
Quality Control: Data analytics can be used to identify trends in defect rates, allowing for proactive adjustments to the production process and prevention of further defects. This may involve analyzing the characteristics of defective products to pinpoint the source of the problem.
Risks and Mitigations:
-
Data Silos: Data scattered across different systems can hinder effective analysis. Integrating data into a unified system is crucial.
-
Data Quality: Inaccurate or incomplete data can lead to flawed analyses and ineffective improvement strategies. Implementing data validation and quality control measures is important.
-
Lack of Expertise: Analyzing manufacturing data effectively often requires specialized skills and expertise. Training personnel or engaging data scientists may be necessary.
Impact and Implications:
Data analytics provides the foundation for a data-driven approach to yield improvement. This enables manufacturers to move beyond reactive problem-solving and proactively optimize their processes for increased efficiency and profitability.
Conclusion: Reinforcing the Connection:
The interplay between data analytics and yield highlights the power of data-driven decision-making in manufacturing. By leveraging data effectively, manufacturers can significantly improve yield, reduce costs, enhance quality, and gain a competitive edge.
Further Analysis: Examining Data Analytics in Greater Detail:
Data analytics techniques like regression analysis, statistical process control, and machine learning algorithms offer increasingly sophisticated ways to analyze manufacturing data and improve yield. These techniques provide actionable insights that enable manufacturers to precisely identify areas for improvement and implement targeted interventions.
FAQ Section: Answering Common Questions About Yield in Manufacturing:
Q: What is the difference between first-pass yield and rolled throughput yield?
A: First-pass yield (FPY) measures the percentage of good units produced in a single stage without rework. Rolled throughput yield (RTY) calculates the cumulative yield across multiple stages, accounting for the cascading effect of defects.
Q: How can I improve yield in my manufacturing process?
A: Improving yield requires a multifaceted approach focusing on process optimization, preventative maintenance, quality control enhancements, employee training, and the implementation of Lean manufacturing principles.
Q: What is the role of data analytics in yield improvement?
A: Data analytics helps identify patterns and root causes of defects, enabling proactive adjustments to the process and resulting in improved yield.
Practical Tips: Maximizing the Benefits of Yield Improvement:
-
Establish Clear Yield Goals: Define specific, measurable, achievable, relevant, and time-bound (SMART) goals for yield improvement.
-
Implement a Robust Data Collection System: Ensure reliable data collection across all relevant processes.
-
Analyze Data Regularly: Conduct regular data analysis to identify trends and areas for improvement.
-
Implement Preventative Maintenance: Schedule regular equipment maintenance to prevent downtime.
-
Continuously Improve Processes: Use Lean methodologies and Kaizen events to drive continuous improvement.
Final Conclusion: Wrapping Up with Lasting Insights:
Yield in manufacturing is a critical metric reflecting operational efficiency and profitability. By understanding different types of yield, identifying factors influencing it, and implementing effective improvement strategies, manufacturers can significantly enhance their performance, reduce costs, and improve customer satisfaction. The strategic application of data analytics further empowers manufacturers to move towards a data-driven, proactive approach to continuous yield improvement, ensuring long-term competitiveness and success.
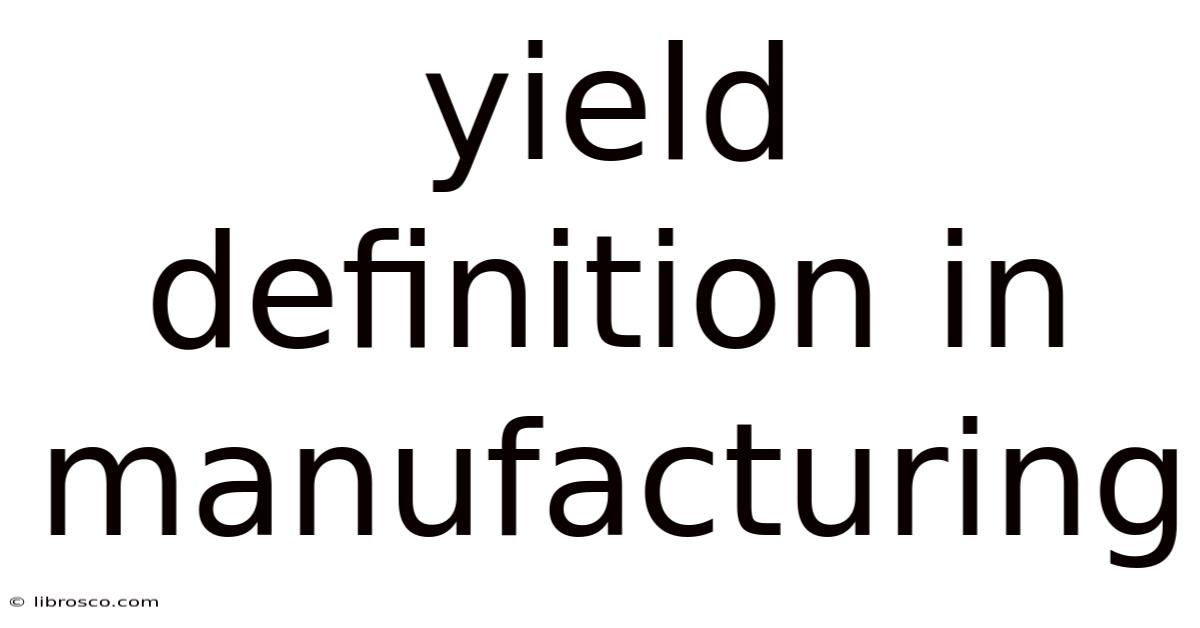
Thank you for visiting our website wich cover about Yield Definition In Manufacturing. We hope the information provided has been useful to you. Feel free to contact us if you have any questions or need further assistance. See you next time and dont miss to bookmark.
Also read the following articles
Article Title | Date |
---|---|
Does Chase Credit Card Have A Grace Period | Apr 02, 2025 |
What Is Kovo Credit Line Reviews | Apr 02, 2025 |
Late Fees Colorado Rent | Apr 02, 2025 |
Kovo Credit Builder Review | Apr 02, 2025 |
Apa Itu Blockbuster | Apr 02, 2025 |