Work Practice Control Definition
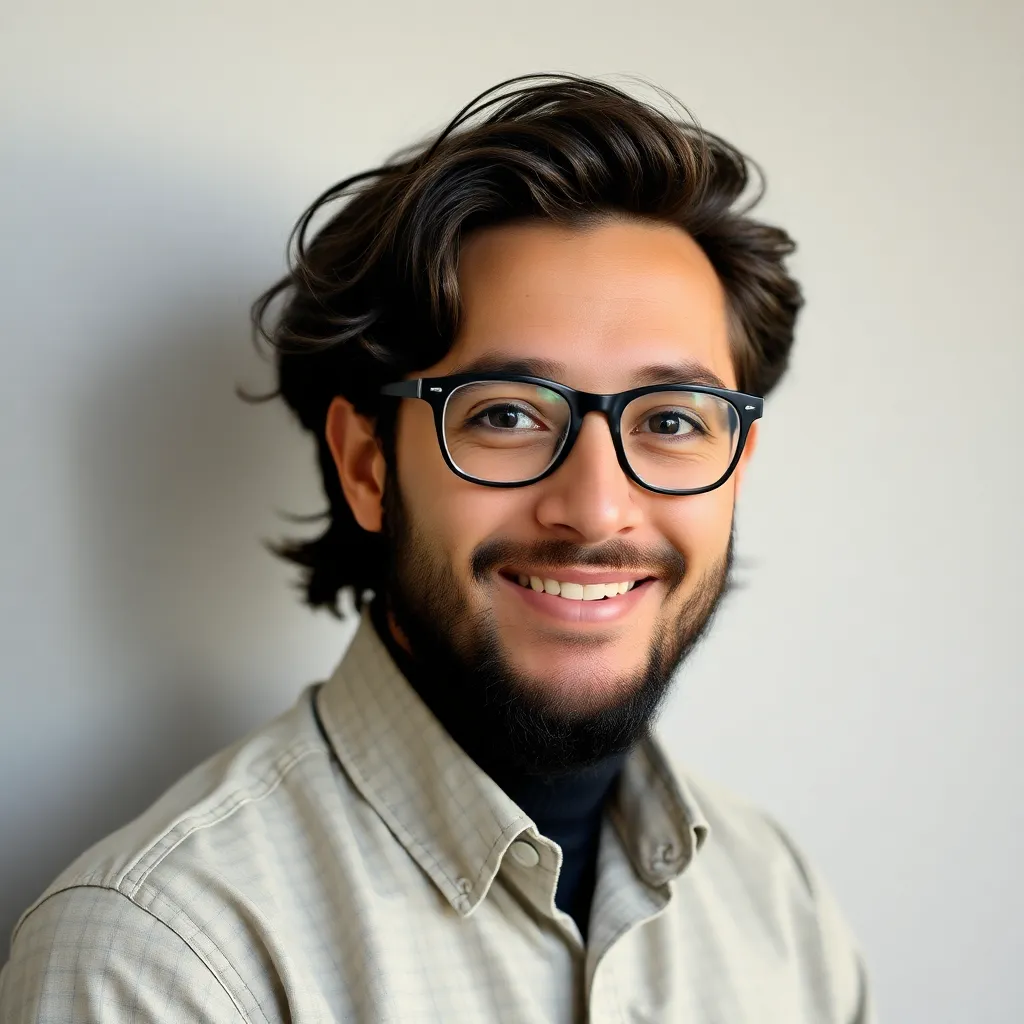
adminse
Apr 01, 2025 · 8 min read

Table of Contents
Mastering the Workplace: A Deep Dive into Work Practice Control Definition
What if the future of workplace safety and efficiency hinges on a clear understanding of work practice controls? This critical concept is paramount to minimizing risks, maximizing productivity, and fostering a thriving work environment.
Editor’s Note: This comprehensive article on work practice controls was published today, providing you with the latest insights and best practices for implementing effective control measures in your workplace.
Why Work Practice Controls Matter:
Work practice controls are fundamental to a robust occupational safety and health (OSH) program. They represent a proactive approach to risk mitigation, addressing potential hazards by modifying the way tasks are performed. Unlike engineering controls which alter the workplace environment, or administrative controls which modify work schedules, work practice controls focus on the how of the job. This makes them a crucial component of a layered safety approach, supplementing and reinforcing other control measures. Their relevance spans diverse industries, from manufacturing and construction to healthcare and IT, impacting productivity, employee well-being, and legal compliance. They are essential for reducing workplace incidents, lowering insurance premiums, and improving overall organizational performance. Furthermore, a strong work practice control system demonstrates a commitment to employee safety, enhancing morale and fostering a positive work culture.
Overview: What This Article Covers:
This article provides a comprehensive exploration of work practice controls, examining their definition, types, implementation, and integration within a broader OSH framework. It will delve into specific examples, address common challenges, and offer practical advice for maximizing their effectiveness. Readers will gain a thorough understanding of how to implement, maintain, and improve work practice controls within their respective workplaces.
The Research and Effort Behind the Insights:
This article is the result of extensive research, drawing upon established OSH standards, industry best practices, and real-world case studies. Information sourced from organizations like OSHA (Occupational Safety and Health Administration), NIOSH (National Institute for Occupational Safety and Health), and relevant industry associations ensures accuracy and reliability. The analysis presented aims to provide actionable, data-driven insights that can be directly applied to improve workplace safety and efficiency.
Key Takeaways:
- Definition and Core Concepts: A detailed explanation of work practice controls and their relationship to other control measures.
- Types of Work Practice Controls: Categorization and examples of various types, including safe operating procedures, personal protective equipment (PPE) usage, and ergonomics.
- Implementation Strategies: A step-by-step guide to effectively implementing work practice controls, including training, monitoring, and reinforcement.
- Challenges and Solutions: Identifying common obstacles in implementing and maintaining work practice controls and strategies for overcoming them.
- Integration with Other Control Measures: Understanding how work practice controls fit within a layered safety approach.
- Measuring Effectiveness: Methods for evaluating the success of implemented work practice controls.
Smooth Transition to the Core Discussion:
Having established the importance of work practice controls, let's now delve into the specifics, exploring their definition, categories, and practical application within various workplace settings.
Exploring the Key Aspects of Work Practice Controls:
1. Definition and Core Concepts:
Work practice controls are methods used to modify how a job is performed to minimize or eliminate employee exposure to hazards. They focus on the behavior and actions of workers, aiming to prevent unsafe practices and promote safe work habits. Unlike engineering controls that alter the workplace itself (e.g., ventilation systems), or administrative controls that adjust work schedules or procedures (e.g., job rotation), work practice controls target the worker's interaction with the hazard. They are often the last line of defense when engineering and administrative controls are insufficient or impractical.
2. Types of Work Practice Controls:
Several categories of work practice controls exist, each addressing specific aspects of workplace safety:
- Safe Operating Procedures (SOPs): These are documented step-by-step instructions for performing tasks safely. SOPs detail proper procedures, potential hazards, and safety precautions. They are essential for ensuring consistency and minimizing errors.
- Personal Protective Equipment (PPE) Usage: Proper selection, use, maintenance, and disposal of PPE (e.g., gloves, safety glasses, respirators) are crucial work practice controls. Effective training and enforcement are necessary to ensure PPE is used correctly.
- Ergonomics: Ergonomic work practices focus on designing workspaces and tasks to minimize physical strain and injuries. This includes proper posture, lifting techniques, and workstation adjustments.
- Housekeeping: Maintaining a clean and organized workspace is crucial to prevent slips, trips, and falls, and to reduce the risk of fires and other hazards.
- Lockout/Tagout (LOTO): LOTO procedures ensure that equipment is de-energized and locked out before maintenance or repair to prevent accidental energization and injuries.
- Emergency Procedures: Clear and well-practiced emergency procedures, including evacuation plans and first aid response, are vital work practice controls.
3. Implementation Strategies:
Implementing effective work practice controls requires a structured approach:
- Hazard Identification and Risk Assessment: Thoroughly identify potential hazards and assess their risks to workers.
- Development of SOPs: Create detailed, easy-to-understand SOPs for each task.
- Training and Education: Provide comprehensive training to all employees on proper work practices and the use of PPE.
- Monitoring and Enforcement: Regularly monitor employee compliance with SOPs and work practices. Consequences should be in place for non-compliance.
- Feedback and Improvement: Solicit employee feedback to identify areas for improvement and regularly review and update SOPs as needed.
4. Challenges and Solutions:
Implementing and maintaining work practice controls can present challenges:
- Resistance to Change: Employees may resist new procedures or practices. Addressing concerns and emphasizing the benefits of safe work practices is crucial.
- Lack of Training: Inadequate training can lead to inconsistent application of controls. Comprehensive and regular training is essential.
- Enforcement Difficulties: Enforcing work practice controls consistently can be challenging. Clear consequences for non-compliance are necessary.
- Cost and Time: Implementing and maintaining controls can require investment in time and resources. Cost-benefit analysis can help justify the investment.
5. Integration with Other Control Measures:
Work practice controls should be integrated with other control measures to create a layered safety approach. Engineering controls (e.g., machine guarding) should be the primary control, followed by administrative controls (e.g., job rotation), with work practice controls as a final layer of protection. This layered approach provides redundancy and ensures maximum protection.
6. Measuring Effectiveness:
The effectiveness of work practice controls should be regularly evaluated through:
- Incident Rates: Tracking the number of workplace injuries and illnesses.
- Observation and Audits: Regularly observing employee work practices and conducting audits to identify areas for improvement.
- Employee Feedback: Gathering feedback from employees on the effectiveness of controls.
Closing Insights: Summarizing the Core Discussion:
Work practice controls are not simply a set of rules; they are a proactive and essential element of a comprehensive OSH program. By implementing effective controls, organizations can create safer, more productive, and more compliant workplaces. Their effectiveness hinges on proper planning, implementation, monitoring, and continuous improvement.
Exploring the Connection Between Training and Work Practice Controls:
Effective training is inextricably linked to successful work practice control implementation. Training serves as the bridge between established safety procedures and actual employee behavior. Without adequate training, even the most robust SOPs will remain ineffective.
Key Factors to Consider:
- Roles and Real-World Examples: Training should be tailored to specific job roles and responsibilities. For instance, training for operating heavy machinery would differ significantly from training on safe chemical handling procedures. Real-world examples and scenarios should be incorporated to make the training relevant and engaging.
- Risks and Mitigations: Training should highlight potential risks associated with improper work practices and clearly outline mitigation strategies. This could involve simulations, demonstrations, or interactive exercises.
- Impact and Implications: Employees need to understand the impact of their actions on their own safety and the safety of others. Highlighting the consequences of non-compliance is crucial for reinforcing the importance of safe work practices.
Conclusion: Reinforcing the Connection:
The relationship between training and work practice controls is symbiotic. Effective training empowers employees to follow established procedures correctly, while a robust work practice control system provides the framework for targeted training initiatives. This integrated approach creates a virtuous cycle of continuous improvement, leading to a safer and more efficient workplace.
Further Analysis: Examining Training Methods in Greater Detail:
Several training methods can enhance the effectiveness of work practice controls:
- On-the-Job Training: Direct observation and guidance by experienced workers.
- Classroom Training: Structured lectures and presentations.
- Interactive Training: Simulations, games, and other interactive activities.
- E-learning: Online modules and courses.
FAQ Section: Answering Common Questions About Work Practice Controls:
- What is the difference between work practice controls and engineering controls? Work practice controls focus on modifying worker behavior, while engineering controls modify the workplace environment.
- How often should work practice controls be reviewed? Regular reviews, at least annually, are recommended to ensure they remain effective and relevant.
- What are the consequences of non-compliance with work practice controls? Consequences can range from disciplinary action to serious injury or death.
- How can I ensure employee buy-in for work practice controls? Involve employees in the development and implementation process, address their concerns, and highlight the benefits of safe work practices.
Practical Tips: Maximizing the Benefits of Work Practice Controls:
- Start with a thorough hazard assessment.
- Develop clear and concise SOPs.
- Provide comprehensive training to all employees.
- Regularly monitor compliance.
- Continuously evaluate and improve controls.
Final Conclusion: Wrapping Up with Lasting Insights:
Work practice controls are a cornerstone of a robust occupational safety and health program. By understanding their definition, implementation strategies, and integration with other control measures, organizations can significantly reduce workplace hazards and create a culture of safety and efficiency. Investing in effective work practice controls is not just a matter of compliance; it’s an investment in the well-being and productivity of your workforce. A proactive approach, emphasizing training and continuous improvement, will yield lasting benefits for both employees and the organization.
Latest Posts
Latest Posts
-
How To Change Billing Cycle Of Tata Credit Card
Apr 10, 2025
-
How To Change Billing Cycle Of Indusind Credit Card Online
Apr 10, 2025
-
How To Change Billing Cycle Of Citibank Credit Card
Apr 10, 2025
-
How To Change Billing Cycle Of Bob Credit Card
Apr 10, 2025
-
How To Change Billing Cycle Of Hsbc Credit Card
Apr 10, 2025
Related Post
Thank you for visiting our website which covers about Work Practice Control Definition . We hope the information provided has been useful to you. Feel free to contact us if you have any questions or need further assistance. See you next time and don't miss to bookmark.