What Is The Minimum Cover For Pipework Installed Underneath A Driveway
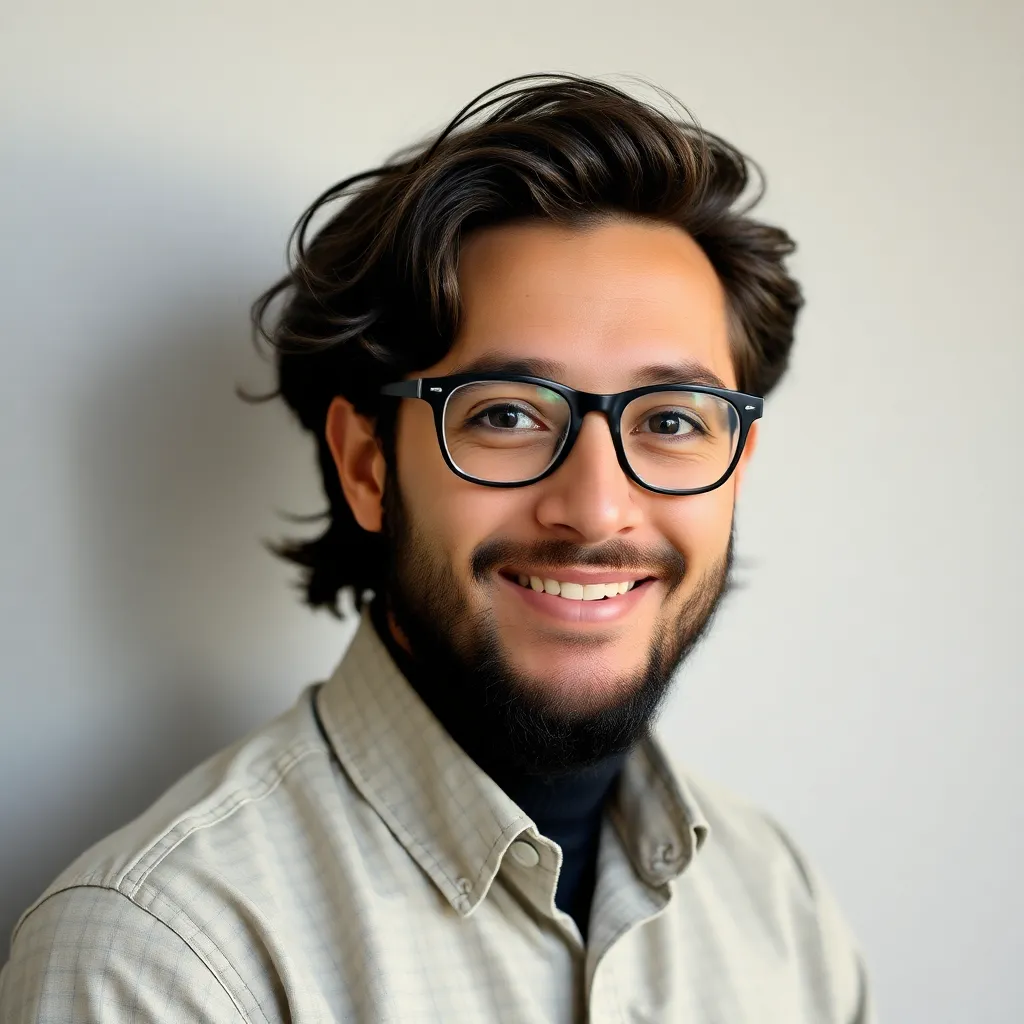
adminse
Apr 05, 2025 · 9 min read
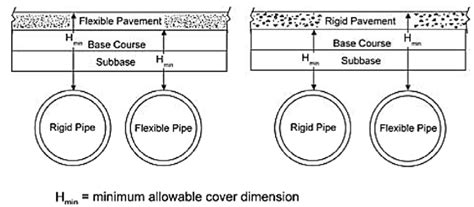
Table of Contents
Uncovering the Minimum Cover for Driveway Pipework: A Comprehensive Guide
What if inadequate pipework cover under your driveway leads to costly repairs and disruptions? Ensuring sufficient cover is crucial for the longevity and safety of your underground utilities.
Editor’s Note: This article on minimum cover for pipework installed underneath driveways has been compiled using current building regulations, industry best practices, and expert insights. The information provided aims to offer a comprehensive understanding of this critical aspect of underground utility installation. However, local regulations may vary, and it's crucial to consult with relevant authorities and qualified professionals before undertaking any work.
Why Sufficient Pipe Cover Matters:
Inadequate cover for underground pipes presents significant risks. Damage from vehicle traffic, frost heave, and accidental excavation are all potential problems that can lead to leaks, burst pipes, and costly repairs. Beyond the financial implications, insufficient cover can cause significant disruption to your property and potentially environmental hazards if the pipe carries hazardous materials. Furthermore, insurance companies often require evidence of compliant installation to validate claims. Proper cover ensures the long-term functionality and safety of your utilities.
Overview: What This Article Covers
This article will provide a thorough examination of the minimum cover requirements for pipes under driveways. We'll explore relevant building regulations, influencing factors such as pipe material and soil type, best practices for installation, and the consequences of insufficient cover. The article will also address frequently asked questions and offer practical advice for homeowners and professionals alike.
The Research and Effort Behind the Insights
This article draws upon extensive research encompassing national and regional building codes, industry standards (such as those from organizations like the American Society of Civil Engineers (ASCE) and relevant national standards bodies), and best practices documented in engineering and construction manuals. The information presented reflects widely accepted industry norms and is intended as a guideline, not a substitute for professional consultation.
Key Takeaways:
- Legal and Regulatory Compliance: Understanding the minimum cover requirements as dictated by local building codes is paramount.
- Material Considerations: The type of pipe material significantly impacts the required cover depth.
- Soil Conditions: Soil type, compaction, and potential for frost heave influence cover depth calculations.
- Installation Techniques: Proper bedding and backfilling techniques are crucial for long-term pipe stability.
- Consequences of Inadequate Cover: Understanding the potential risks of insufficient cover aids in informed decision-making.
Smooth Transition to the Core Discussion:
With an understanding of why sufficient pipe cover is essential, let's delve into the specifics of determining the minimum cover depth required for your driveway pipework.
Exploring the Key Aspects of Minimum Pipe Cover
1. Legal and Regulatory Compliance:
The first and most important step is to consult your local building codes and regulations. These regulations vary by region and jurisdiction, and failure to comply can result in fines, delays, and potential liability issues. The codes typically specify minimum cover depths for different pipe types and applications, considering factors such as traffic load and potential hazards. Always obtain the necessary permits before undertaking any excavation work.
2. Pipe Material and Characteristics:
The material of the pipe itself impacts the required cover depth. For example:
- High-Density Polyethylene (HDPE): Known for its flexibility and resistance to impact, HDPE pipes often require less cover than rigid materials.
- Polyvinyl Chloride (PVC): PVC pipes are durable but less flexible than HDPE, necessitating potentially greater cover.
- Ductile Iron: This robust material is used in high-pressure applications and typically demands substantial cover depth.
- Cast Iron: While durable, cast iron pipes are susceptible to corrosion and require adequate cover to protect against damage.
The pipe's diameter and pressure rating also influence the minimum cover requirements. Larger diameter pipes and those operating under higher pressure usually require deeper burial.
3. Soil Type and Conditions:
The soil's composition and condition are critical factors determining the necessary cover depth. Several aspects come into play:
- Soil Compaction: Well-compacted soil provides better support and can reduce the required cover depth compared to loose, unstable soil.
- Soil Bearing Capacity: The soil's ability to support the load above the pipe influences the necessary depth. Clay soils, for example, might require more cover than sandy soils.
- Frost Susceptibility: In areas prone to frost heave (where freezing and thawing soil expands and contracts), increased cover depth is necessary to protect the pipe from damage caused by soil movement. The depth of frost penetration in your region is a crucial consideration.
- Water Table: A high water table can increase the risk of corrosion and pipe damage. Sufficient cover helps mitigate this risk.
4. Traffic Load:
The type and volume of traffic anticipated over the pipe are significant determinants. Driveways experiencing heavy vehicle traffic require greater cover depths than those used only by light vehicles. The design of the driveway itself and the underlying sub-base materials should also be taken into account. A well-constructed driveway with proper compaction will minimize the load on the pipes.
5. Installation Techniques:
Proper installation techniques are crucial for ensuring the longevity of your pipework. These techniques include:
- Bedding: The pipe should be placed on a stable, compacted bed of granular material (like sand or gravel) to provide even support and prevent point loading.
- Backfilling: The backfill material should be carefully selected and compacted in layers to minimize settlement and protect the pipe from damage. The use of specific backfill materials might be specified in building codes to ensure the structural integrity of the pipe and its surrounding soil.
- Pipe Protection: Protective sleeves or encasements can be used to add an extra layer of protection, particularly in areas with potential for damage from excavation or ground movement.
6. Consequences of Inadequate Cover:
Insufficient cover depth can lead to numerous problems:
- Pipe Damage: Vehicles driving over pipes with insufficient cover can crush or fracture them, causing leaks or complete failure.
- Leaks: Cracks and fissures resulting from inadequate cover allow water to enter the pipe, potentially leading to corrosion, contamination, and structural damage.
- Excavation Damage: Accidental digging near poorly covered pipes can easily cause damage, leading to expensive repairs and service disruptions.
- Frost Heave Damage: In areas with frost, inadequate cover can expose pipes to freeze-thaw cycles, causing them to lift and crack.
- Insurance Claims: Insurance companies typically require evidence of compliant installation before processing claims related to pipe damage.
Closing Insights: Summarizing the Core Discussion:
The minimum cover for pipework installed under a driveway is not a universal figure. It's a critical calculation that requires careful consideration of numerous factors. Ignoring these factors can lead to significant financial and logistical headaches. By understanding and adhering to local regulations, selecting appropriate pipe materials, addressing soil conditions, and utilizing correct installation practices, you can ensure the long-term safety and reliability of your underground utilities.
Exploring the Connection Between Soil Conditions and Minimum Pipe Cover
The relationship between soil conditions and minimum pipe cover is pivotal. Soil's characteristics directly influence the pipe's stability and its resistance to external forces. Different soil types exhibit varying levels of compaction, bearing capacity, and susceptibility to frost heave.
Key Factors to Consider:
- Roles and Real-World Examples: Clay soils, known for their low permeability and high expansion potential upon freezing, require significantly more cover than sandy or gravelly soils. A real-world example is a clay-rich area where frost heave is common. Here, a pipe with minimal cover could be lifted and cracked during winter. Conversely, a well-drained sandy soil might necessitate less cover.
- Risks and Mitigations: Ignoring soil conditions leads to increased risk of pipe damage due to settlement, frost heave, or erosion. Mitigation strategies include thorough soil analysis before installation, utilizing compacted granular backfill, and increasing cover depth to compensate for poor soil conditions.
- Impact and Implications: Improper consideration of soil conditions results in reduced pipe lifespan, increased maintenance costs, potential leaks and disruptions, and possible environmental damage.
Conclusion: Reinforcing the Connection
The interplay between soil conditions and minimum pipe cover is undeniably critical. By conducting a thorough soil assessment and selecting appropriate installation techniques, one can greatly reduce the risk of pipe failure. This ensures the long-term sustainability and reliability of underground pipework.
Further Analysis: Examining Soil Compaction in Greater Detail
Soil compaction refers to the process of reducing the void space within the soil mass. This increases its density and bearing capacity. Proper soil compaction is vital in achieving optimal pipe stability and minimizing settlement after installation. Failure to compact the soil adequately can lead to differential settlement, causing stress on the pipe joints and increasing the risk of failure.
FAQ Section: Answering Common Questions About Minimum Pipe Cover
- What is the typical minimum cover for domestic water pipes under a driveway? There's no single answer; local building codes dictate this. However, depths often range from 0.75 meters to 1.2 meters (2.5 to 4 feet) for driveways with light traffic.
- How does frost depth affect the minimum cover? In frost-prone areas, you need to add the frost depth to the minimum cover to prevent damage from frost heave.
- What type of backfill is recommended? Well-compacted granular materials like sand or gravel are usually recommended.
- Can I install the pipe myself? While you might be able to do some of the work, it's generally recommended to hire a licensed professional plumber to ensure correct installation and compliance with regulations. Incorrect installation invalidates insurance claims.
- What happens if I don't meet the minimum cover requirements? You risk pipe damage, leaks, costly repairs, and potential liability issues.
Practical Tips: Maximizing the Benefits of Adequate Pipe Cover
- Understand the Basics: Consult local building codes and understand the minimum cover requirements for your specific situation.
- Identify Soil Conditions: Conduct a soil analysis to determine the appropriate cover depth based on soil type, compaction, and frost susceptibility.
- Select Appropriate Materials: Choose pipe materials appropriate for your application and soil conditions.
- Use Proper Installation Techniques: Ensure the pipe is correctly bedded and backfilled with appropriate materials and compaction methods.
- Document Your Work: Keep records of the pipe installation, including depths and materials used. This documentation will be invaluable in the event of future repairs or insurance claims.
Final Conclusion: Wrapping Up with Lasting Insights
Ensuring adequate minimum cover for pipework installed under a driveway is not simply a best practice; it's a crucial measure to protect your investment, prevent expensive repairs, and maintain safety. By understanding the various factors influencing cover depth and adhering to local regulations, you can safeguard your property and avoid costly setbacks. Investing in a proper installation is significantly more cost-effective than dealing with the repercussions of inadequate cover.
Latest Posts
Latest Posts
-
How To Activate Navy Federal Credit Card
Apr 06, 2025
-
How To Get Approved For Navy Federal Credit Card
Apr 06, 2025
-
Best Time To Apply For Navy Federal Credit Card
Apr 06, 2025
-
How To Prequalify For Navy Federal Credit Card
Apr 06, 2025
-
How To Apply For Navy Federal Credit Union
Apr 06, 2025
Related Post
Thank you for visiting our website which covers about What Is The Minimum Cover For Pipework Installed Underneath A Driveway . We hope the information provided has been useful to you. Feel free to contact us if you have any questions or need further assistance. See you next time and don't miss to bookmark.