What Is Flexible Manufacturing System
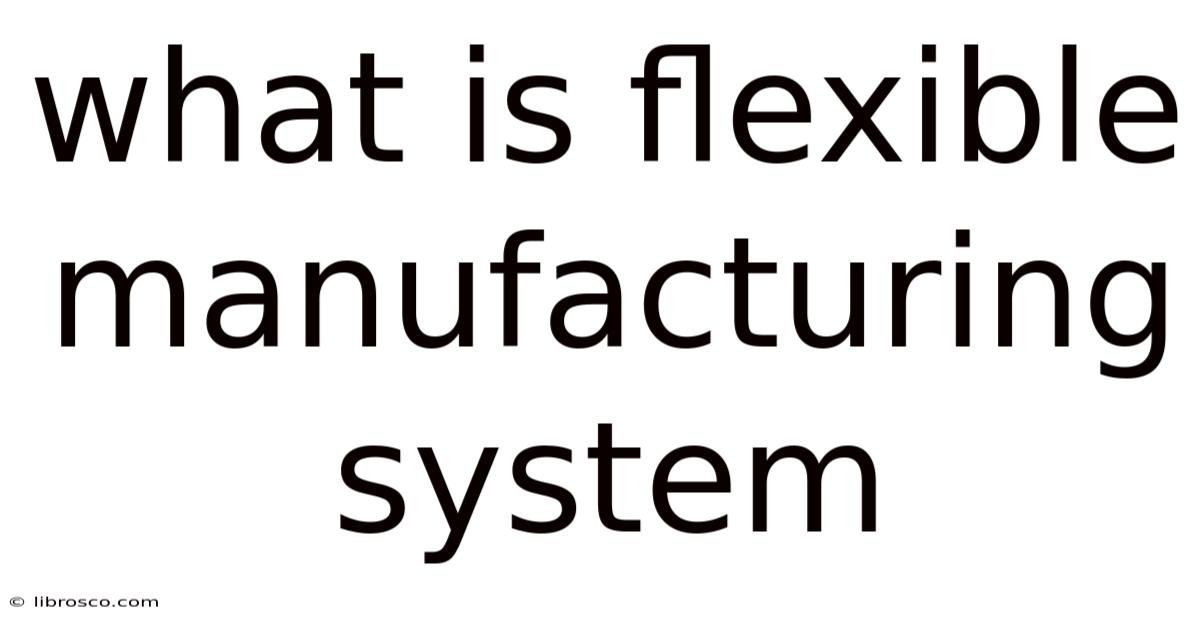
Discover more detailed and exciting information on our website. Click the link below to start your adventure: Visit Best Website meltwatermedia.ca. Don't miss out!
Table of Contents
Unlocking Efficiency: A Deep Dive into Flexible Manufacturing Systems (FMS)
What if the future of manufacturing lies in systems capable of adapting to ever-changing demands? Flexible Manufacturing Systems (FMS) are not just a trend; they are a fundamental shift in how industries produce goods, promising unparalleled efficiency and responsiveness.
Editor’s Note: This article on Flexible Manufacturing Systems (FMS) provides a comprehensive overview of this transformative technology, exploring its components, benefits, challenges, and future implications. The information presented is current and relevant to today's manufacturing landscape.
Why Flexible Manufacturing Systems Matter:
Flexible Manufacturing Systems are revolutionizing manufacturing by enabling companies to produce a wider variety of products with shorter lead times, reduced costs, and increased efficiency. In today's dynamic marketplace, characterized by rapidly changing customer demands and shorter product lifecycles, the ability to adapt quickly is paramount. FMS addresses these challenges head-on, offering a competitive edge to businesses across various sectors, from automotive and electronics to aerospace and pharmaceuticals. The implications extend beyond simple cost savings; FMS facilitates innovation, allows for quicker responses to market trends, and promotes a more sustainable manufacturing approach through minimized waste and optimized resource utilization. Keywords like lean manufacturing, agile manufacturing, automation, computer-integrated manufacturing, and just-in-time manufacturing are all closely related and often implemented in conjunction with FMS.
Overview: What This Article Covers:
This article will delve into the core aspects of Flexible Manufacturing Systems (FMS), providing a detailed understanding of their components, operational principles, advantages, limitations, and future prospects. Readers will gain a comprehensive overview of the technology, including practical applications, implementation strategies, and case studies illustrating real-world success.
The Research and Effort Behind the Insights:
This analysis incorporates insights gathered from extensive research, including academic literature, industry reports, case studies of successful FMS implementations, and interviews with manufacturing experts. The information presented is grounded in credible data and aims to provide readers with accurate and insightful knowledge about FMS.
Key Takeaways:
- Definition and Core Concepts: A clear explanation of FMS, its underlying principles, and key components.
- Components of an FMS: Detailed descriptions of the hardware and software elements essential to a functional FMS.
- Types of FMS: Exploration of various FMS configurations and their suitability for different manufacturing scenarios.
- Advantages of FMS: A comprehensive overview of the benefits, including increased flexibility, efficiency, and reduced costs.
- Challenges of Implementing FMS: A realistic assessment of the hurdles, such as high initial investment and complexity.
- Future Trends in FMS: A look at the evolving landscape of FMS, including advancements in AI, IoT, and robotics.
Smooth Transition to the Core Discussion:
Having established the significance of FMS, we now turn our attention to a more in-depth exploration of its constituent elements, operational principles, and practical applications within various industrial settings.
Exploring the Key Aspects of Flexible Manufacturing Systems:
1. Definition and Core Concepts:
A Flexible Manufacturing System (FMS) is an automated production system designed to efficiently manufacture a variety of products with minimal changeover time. Unlike traditional manufacturing lines that are typically dedicated to a single product or a limited range of products, FMS utilizes Computer Numerical Control (CNC) machines, automated material handling systems, and sophisticated software to adapt to changing production requirements. This adaptability is crucial in responding to fluctuating demand, customizing products, and introducing new product lines quickly. The core concept revolves around flexibility, achieved through automated processes and intelligent control systems.
2. Components of an FMS:
A typical FMS comprises several key components working in concert:
- CNC Machines: These programmable machines form the heart of the system, performing various operations such as milling, drilling, turning, and grinding. Their programmability allows them to adapt to different product designs without manual intervention.
- Automated Material Handling System (AMHS): This system, typically composed of Automated Guided Vehicles (AGVs), conveyor belts, and robots, moves workpieces between machines efficiently and automatically. This eliminates manual handling, reducing lead times and errors.
- Central Computer Control System: This sophisticated software system orchestrates the entire FMS, managing production schedules, monitoring machine status, coordinating material flow, and optimizing the overall production process.
- Tooling and Fixturing: Specialized tooling and fixtures are essential for efficient processing of different parts. These must be easily interchangeable to adapt to the varying needs of different product designs.
- Supervisory Control System: This layer provides real-time monitoring, diagnostics, and control of the entire FMS. It helps optimize performance and detect potential issues early on.
3. Types of FMS:
Several types of FMS exist, each tailored to specific manufacturing needs:
- Cellular Manufacturing Systems: These systems group machines into cells, each dedicated to a family of parts with similar processing requirements. This enhances efficiency by minimizing material handling between machines within the cell.
- Transfer Lines with Flexible Routing: These systems offer a degree of flexibility by allowing workpieces to follow different routes through the production line, depending on the product being manufactured.
- Completely Flexible Systems: These highly adaptable systems can handle a wide range of products with minimal reconfiguration. They typically involve advanced software and sophisticated material handling systems.
4. Advantages of FMS:
The benefits of implementing an FMS are substantial:
- Increased Flexibility: FMS can adapt to changing product designs and demand fluctuations quickly, making them ideal for industries with diverse product lines or frequent product introductions.
- Improved Efficiency: Automation minimizes manual handling and reduces production times, leading to significant efficiency gains.
- Reduced Lead Times: Shorter production cycles translate to faster delivery times, meeting customer demands more effectively.
- Lower Costs: While the initial investment is high, FMS ultimately reduces production costs through increased efficiency and reduced waste.
- Enhanced Quality: Automated processes minimize errors and ensure consistent product quality.
- Better Inventory Management: Just-in-time manufacturing principles can be readily integrated with FMS, minimizing inventory holding costs.
5. Challenges of Implementing FMS:
Despite the significant advantages, implementing an FMS presents several challenges:
- High Initial Investment: The cost of acquiring and installing the necessary hardware and software can be substantial.
- Complexity: Designing, implementing, and maintaining an FMS requires specialized expertise and careful planning.
- Integration Difficulties: Integrating different components of the system can be complex and time-consuming.
- Maintenance and Repair: Downtime due to equipment failure can be costly, requiring robust maintenance and repair procedures.
- Skills Gap: Operating and maintaining an FMS requires skilled personnel, potentially creating a skills gap in the workforce.
6. Impact on Innovation:
FMS facilitates innovation by enabling companies to experiment with new product designs and manufacturing processes more easily. The flexibility inherent in the system allows for quicker prototyping and testing, accelerating the pace of innovation.
Closing Insights: Summarizing the Core Discussion:
Flexible Manufacturing Systems represent a powerful approach to manufacturing, offering significant advantages in terms of flexibility, efficiency, and cost reduction. However, the successful implementation of an FMS requires careful planning, substantial investment, and skilled personnel. By addressing the challenges and leveraging the benefits, companies can achieve a competitive advantage in today's dynamic marketplace.
Exploring the Connection Between Automation and Flexible Manufacturing Systems:
Automation is the cornerstone of FMS. Without sophisticated automation technologies, the flexibility and efficiency gains promised by FMS would be impossible to achieve. The relationship is synergistic; FMS relies on automation to function, while automation's potential is fully realized within the context of a flexible manufacturing environment.
Key Factors to Consider:
- Roles and Real-World Examples: Automation in FMS encompasses robotic arms for material handling, CNC machines programmed for various tasks, and automated guided vehicles for transporting materials. Automakers like Toyota have extensively used FMS to streamline production, achieving significant efficiency gains.
- Risks and Mitigations: Over-reliance on automation can create vulnerabilities. Robust maintenance programs, backup systems, and skilled personnel are crucial to mitigate the risks of downtime.
- Impact and Implications: The impact of automation on FMS is transformative, leading to higher productivity, improved quality, and enhanced competitiveness. However, it also raises concerns about job displacement and the need for workforce reskilling.
Conclusion: Reinforcing the Connection:
The inseparable link between automation and FMS highlights the transformative potential of integrated manufacturing systems. By strategically leveraging automation within the framework of FMS, manufacturers can optimize their operations, enhance their competitive positioning, and achieve sustainable growth.
Further Analysis: Examining Automation in Greater Detail:
The level of automation within an FMS can vary significantly, ranging from partially automated systems to fully automated factories. The optimal level of automation depends on factors like production volume, product complexity, and budget constraints. Advances in robotics, artificial intelligence (AI), and the Internet of Things (IoT) are continually pushing the boundaries of automation within FMS, leading to even greater flexibility and efficiency.
FAQ Section: Answering Common Questions About Flexible Manufacturing Systems:
- What is the difference between FMS and traditional manufacturing? Traditional manufacturing often involves dedicated production lines for specific products, while FMS allows for the production of a variety of products on the same line with minimal changeover.
- How much does it cost to implement an FMS? The cost varies widely depending on the size and complexity of the system, but it represents a significant upfront investment.
- What are the key success factors for FMS implementation? Careful planning, skilled personnel, robust maintenance programs, and effective integration of different components are critical.
- What are the future trends in FMS? The integration of AI, IoT, and advanced robotics is expected to further enhance the flexibility and efficiency of FMS in the years to come.
Practical Tips: Maximizing the Benefits of Flexible Manufacturing Systems:
- Conduct a thorough feasibility study: Assess your manufacturing needs, production volume, and budget constraints before committing to an FMS.
- Select the right technology: Choose components and software that are appropriate for your specific requirements.
- Invest in skilled personnel: Train your workforce to operate and maintain the FMS effectively.
- Implement robust maintenance procedures: Regular maintenance is essential to minimize downtime and ensure the longevity of the system.
- Monitor and optimize performance: Continuously track key metrics and make adjustments as needed to maximize efficiency.
Final Conclusion: Wrapping Up with Lasting Insights:
Flexible Manufacturing Systems represent a paradigm shift in manufacturing, offering a pathway to enhanced flexibility, efficiency, and competitiveness. By embracing the opportunities and addressing the challenges associated with FMS implementation, manufacturers can unlock significant value and secure their position in the evolving global marketplace. The future of manufacturing is flexible, adaptable, and driven by intelligent automation, and FMS is at the forefront of this transformation.
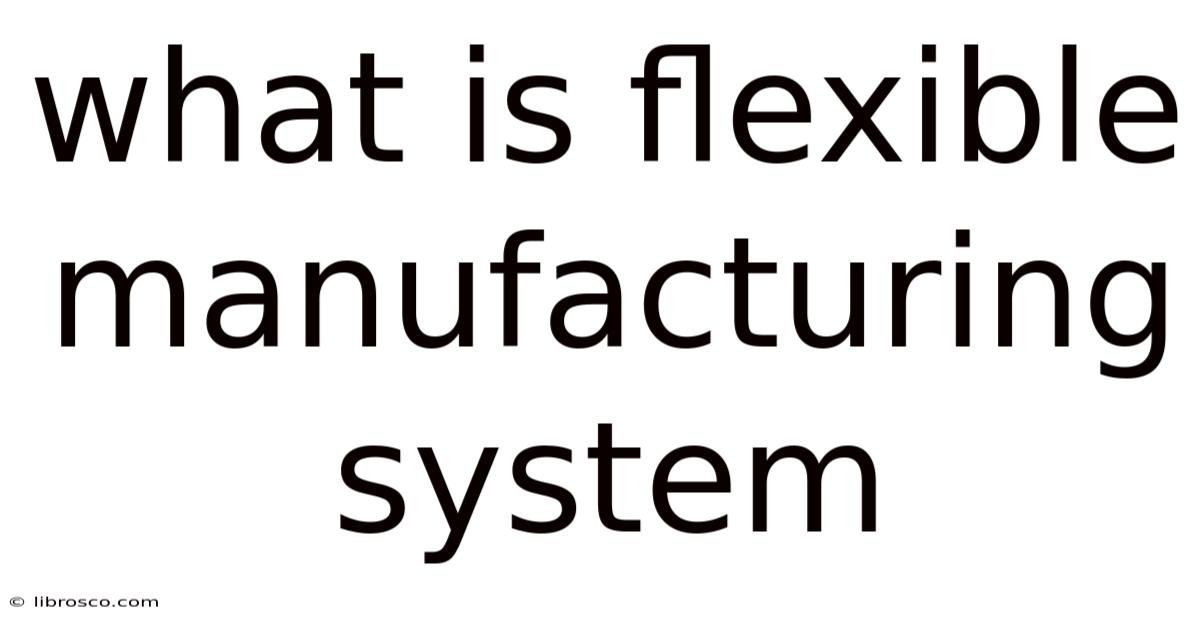
Thank you for visiting our website wich cover about What Is Flexible Manufacturing System. We hope the information provided has been useful to you. Feel free to contact us if you have any questions or need further assistance. See you next time and dont miss to bookmark.
Also read the following articles
Article Title | Date |
---|---|
How To Market Yourself As A Financial Advisor | Apr 29, 2025 |
Shelf Offerings Are Covered Under | Apr 29, 2025 |
How Much Is Auto Insurance Per Month In Texas | Apr 29, 2025 |
How Emv Is Calculated | Apr 29, 2025 |
Faang Meaning Slang | Apr 29, 2025 |