What Is Direct Cost In Manufacturing
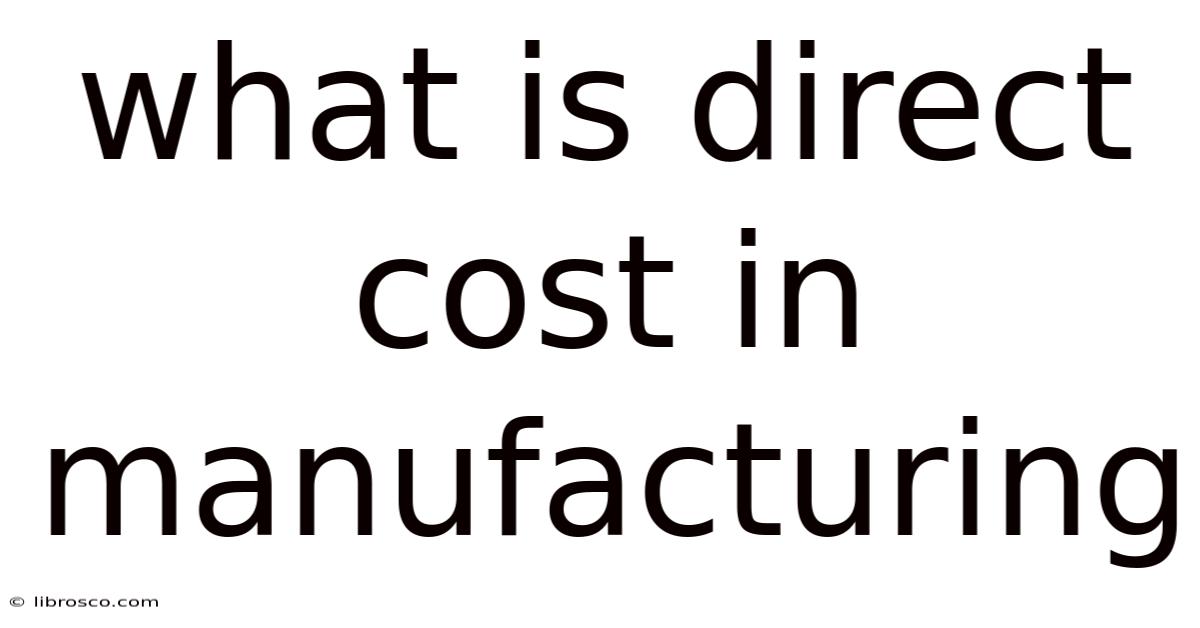
Discover more detailed and exciting information on our website. Click the link below to start your adventure: Visit Best Website meltwatermedia.ca. Don't miss out!
Table of Contents
Decoding Direct Costs in Manufacturing: A Comprehensive Guide
What if understanding direct costs is the key to unlocking manufacturing profitability? Mastering direct cost management is paramount for any manufacturer aiming for sustainable growth and competitive advantage.
Editor’s Note: This article on direct costs in manufacturing was published today, providing you with the most up-to-date information and insights to optimize your manufacturing processes.
Why Direct Costs Matter: Relevance, Practical Applications, and Industry Significance
Direct costs are the lifeblood of any manufacturing operation. Understanding and effectively managing them is not merely an accounting exercise; it’s a strategic imperative. Accurate direct cost calculation directly impacts pricing strategies, profitability assessments, and ultimately, the long-term viability of a manufacturing business. From small-scale workshops to large-scale industrial plants, the principles remain consistent: knowing what constitutes a direct cost is crucial for informed decision-making. Improper cost allocation can lead to underpricing, reduced profit margins, and ultimately, business failure. This article will equip you with the knowledge to accurately identify, track, and manage these critical expenses.
Overview: What This Article Covers
This article provides a comprehensive overview of direct costs in manufacturing. We will delve into the core definition, explore various examples across different industries, discuss the challenges in accurate cost allocation, and offer practical strategies for effective management. We will also examine the relationship between direct costs and other cost categories, including indirect costs and overhead. Finally, we will explore how effective direct cost management contributes to a manufacturing business's overall success.
The Research and Effort Behind the Insights
This article is the result of extensive research, drawing upon established accounting principles, industry best practices, and real-world case studies. The information presented is supported by credible sources, ensuring readers receive accurate and reliable guidance.
Key Takeaways:
- Definition and Core Concepts: A clear explanation of direct costs and their distinction from indirect costs.
- Practical Applications: Real-world examples of direct costs across various manufacturing sectors.
- Challenges and Solutions: Common pitfalls in direct cost accounting and strategies for overcoming them.
- Future Implications: The evolving role of direct cost management in the context of technological advancements and global competition.
Smooth Transition to the Core Discussion
Now that we understand the overarching importance of direct cost management, let's delve into the specifics. We'll start by defining what constitutes a direct cost and then explore its various components in detail.
Exploring the Key Aspects of Direct Costs in Manufacturing
1. Definition and Core Concepts:
A direct cost is any expense directly traceable to the production of goods. This means the cost can be specifically identified and attributed to a particular product or unit of output. It's a cost that would not exist if that specific product were not being manufactured. This contrasts sharply with indirect costs (overhead), which are more broadly applied across the entire manufacturing process and are difficult to specifically allocate to individual products.
2. Key Components of Direct Costs:
Direct costs typically comprise two major elements:
-
Direct Materials: These are the raw materials, components, and supplies that become an integral part of the finished product. Examples include:
- Steel for automotive manufacturing
- Wood for furniture manufacturing
- Fabric for garment manufacturing
- Silicon for semiconductor manufacturing
- Chemicals for pharmaceutical manufacturing
- Plastic resins for packaging production
The cost of direct materials includes the purchase price, freight charges, and any applicable taxes. Careful inventory management and efficient procurement strategies are crucial for controlling direct material costs.
-
Direct Labor: This encompasses the wages, salaries, and benefits paid to employees directly involved in the production process. This includes assembly line workers, machine operators, and quality control inspectors who directly contribute to the creation of the finished product. It excludes the salaries of administrative staff, marketing personnel, or upper management. Accurate time tracking and efficient labor scheduling are essential for managing direct labor costs.
3. Applications Across Industries:
The application of direct cost principles remains consistent across diverse manufacturing sectors, though the specific items classified as direct costs will vary.
- Automotive Manufacturing: Direct costs include steel, rubber, glass, electronics, and the wages of assembly line workers.
- Food Processing: Direct costs encompass raw ingredients (meat, vegetables, grains), packaging materials, and the labor of production line employees.
- Pharmaceutical Manufacturing: Direct costs consist of raw chemicals, active pharmaceutical ingredients, packaging, and the wages of scientists and technicians directly involved in production.
- Textile Manufacturing: Direct costs include fibers, dyes, and the wages of textile workers.
4. Challenges and Solutions:
Accurate allocation of direct costs can be challenging. Several factors can complicate the process:
- Joint Products: When a single manufacturing process produces multiple products simultaneously, allocating direct costs to each individual product can be complex. Appropriate allocation methods (e.g., market value, physical quantity) need to be employed.
- Indirect Labor Costs: Distinguishing between direct and indirect labor can be tricky, particularly in smaller manufacturing operations where employees may perform multiple tasks. Clear job descriptions and accurate time tracking are essential.
- Waste and Spoilage: Materials lost due to spoilage or defective products represent a direct cost that needs to be accounted for. Minimizing waste through efficient processes is crucial for cost control.
5. Impact on Innovation:
Effective direct cost management fosters innovation. By accurately tracking and analyzing direct costs, manufacturers can identify areas for improvement, streamlining processes and reducing waste. This allows for investment in more efficient equipment, automation, and new technologies, leading to increased productivity and competitiveness.
Closing Insights: Summarizing the Core Discussion
Understanding direct costs is fundamental to successful manufacturing. By accurately identifying and managing these costs, businesses can optimize their pricing strategies, enhance profitability, and gain a competitive edge. The principles discussed apply universally, irrespective of the specific industry or scale of operation.
Exploring the Connection Between Inventory Management and Direct Costs
Inventory management is intrinsically linked to direct costs. Efficient inventory control minimizes waste, reduces storage costs, and ensures the timely availability of direct materials. Inefficient inventory management can lead to increased holding costs, stockouts, and ultimately, higher direct costs.
Key Factors to Consider:
- Roles and Real-World Examples: Poor inventory control can result in obsolete stock, leading to write-offs and increased direct material costs. Effective inventory management, using methods like Just-in-Time (JIT) inventory, minimizes waste and holding costs.
- Risks and Mitigations: Stockouts can halt production, leading to lost sales and potentially higher labor costs due to idle time. Accurate demand forecasting and robust safety stock levels can mitigate this risk.
- Impact and Implications: Accurate inventory management directly influences the cost of goods sold (COGS), impacting profitability and pricing decisions.
Conclusion: Reinforcing the Connection
The relationship between inventory management and direct costs is symbiotic. Efficient inventory practices are essential for controlling direct costs and maintaining a competitive edge. Effective inventory management leads to optimized production, reduced waste, and improved profitability.
Further Analysis: Examining Inventory Management in Greater Detail
Different inventory management techniques—FIFO (First-In, First-Out), LIFO (Last-In, First-Out), and weighted average cost—impact how direct material costs are accounted for. The choice of method affects the reported cost of goods sold and ultimately, the profitability of the manufacturing business. Understanding these methods is crucial for accurate financial reporting and strategic decision-making.
FAQ Section: Answering Common Questions About Direct Costs in Manufacturing
Q: What is the difference between direct and indirect costs?
A: Direct costs are directly traceable to the production of goods, while indirect costs (overhead) are shared across multiple products and are difficult to allocate specifically.
Q: How are direct costs calculated?
A: Direct costs are calculated by summing the cost of direct materials and direct labor used in production.
Q: What is the importance of accurate direct cost accounting?
A: Accurate direct cost accounting is essential for accurate pricing, profitability analysis, and informed decision-making.
Q: How can businesses improve their direct cost management?
A: Businesses can improve direct cost management through efficient inventory management, optimized production processes, and effective labor scheduling.
Practical Tips: Maximizing the Benefits of Direct Cost Management
- Implement robust inventory management systems: Utilize inventory tracking software and employ methods like JIT to minimize waste and storage costs.
- Streamline production processes: Identify and eliminate bottlenecks in the production line to reduce idle time and labor costs.
- Negotiate favorable terms with suppliers: Secure competitive pricing on direct materials through strong supplier relationships.
- Invest in employee training and development: Enhance employee skills to improve productivity and reduce waste.
- Regularly review and analyze direct cost data: Track key metrics and identify areas for improvement through data-driven decision-making.
Final Conclusion: Wrapping Up with Lasting Insights
Understanding and effectively managing direct costs is a cornerstone of successful manufacturing. By meticulously tracking expenses, optimizing processes, and implementing robust management systems, manufacturers can enhance profitability, gain a competitive advantage, and ensure long-term sustainability. The information presented in this article provides a solid foundation for navigating the complexities of direct cost accounting and leveraging its power for strategic growth.
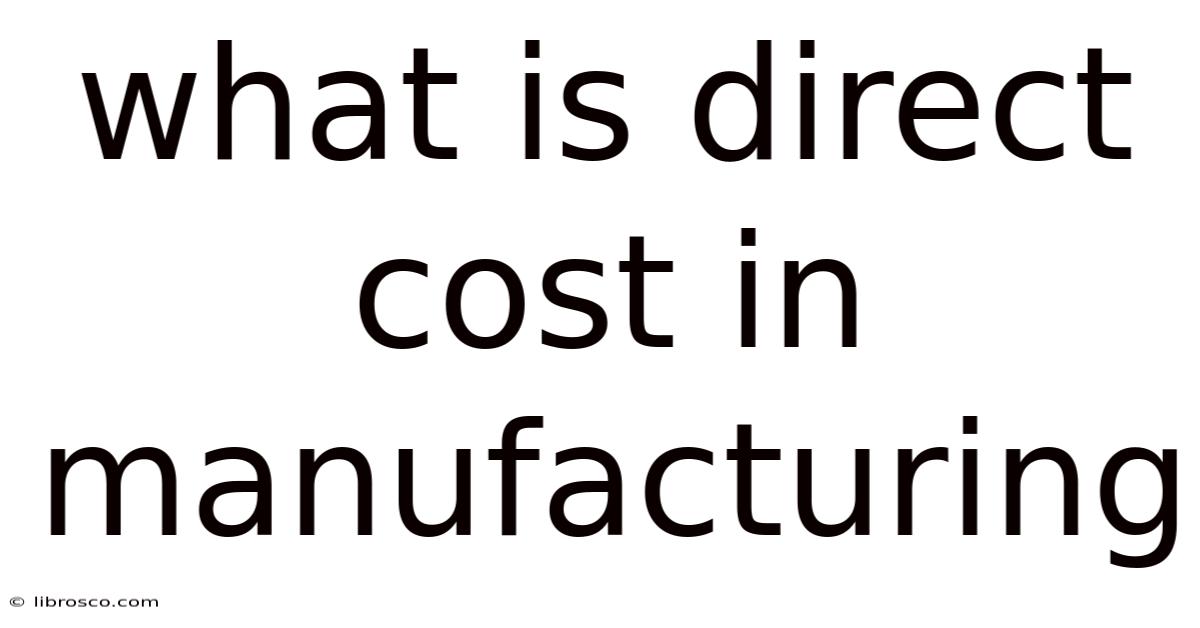
Thank you for visiting our website wich cover about What Is Direct Cost In Manufacturing. We hope the information provided has been useful to you. Feel free to contact us if you have any questions or need further assistance. See you next time and dont miss to bookmark.
Also read the following articles
Article Title | Date |
---|---|
Factor Markets Ap Microeconomics | Apr 27, 2025 |
Market Value Of Firms Equity Formula | Apr 27, 2025 |
How Long Do I Have To File A Gap Insurance Claim | Apr 27, 2025 |
Bust Out Fraud Algorithm | Apr 27, 2025 |
Dp3 Insurance Coverage | Apr 27, 2025 |