What Is Direct Cost In Construction
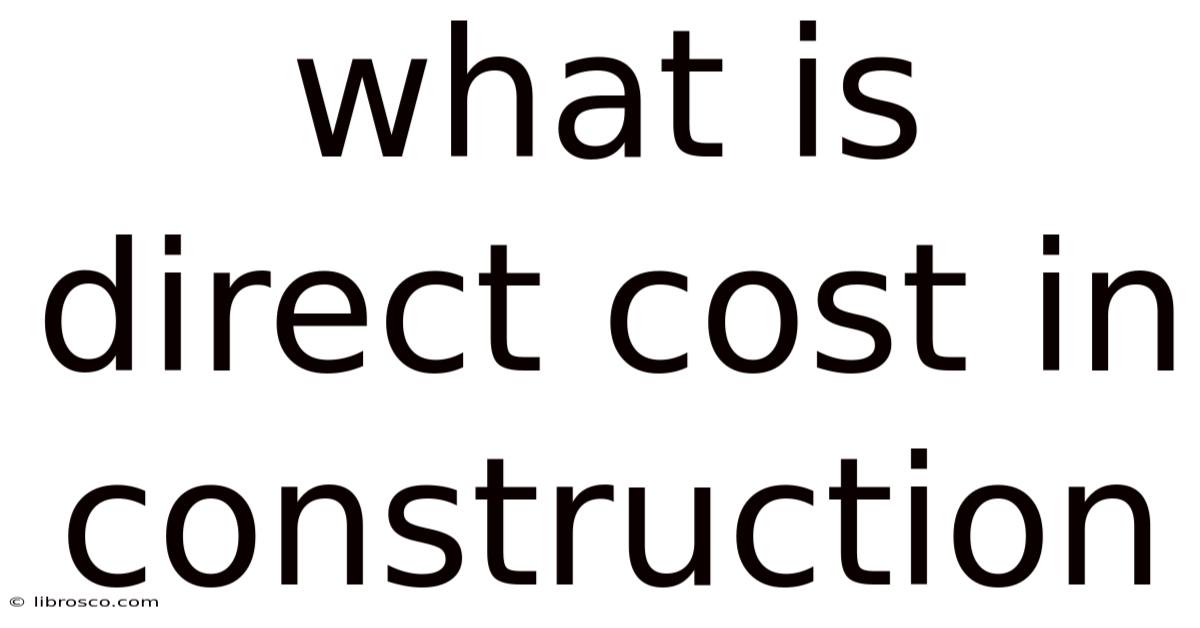
Discover more detailed and exciting information on our website. Click the link below to start your adventure: Visit Best Website meltwatermedia.ca. Don't miss out!
Table of Contents
Decoding Direct Costs in Construction: A Comprehensive Guide
What if the true profitability of a construction project hinges on accurately understanding direct costs? Mastering this crucial element is the cornerstone of successful project management and financial stability.
Editor’s Note: This article on direct costs in construction was published today, providing you with the most up-to-date insights and best practices in the field. Understanding direct costs is vital for any contractor, project manager, or stakeholder involved in the construction industry.
Why Direct Costs Matter: Relevance, Practical Applications, and Industry Significance
Direct costs represent the lifeblood of any construction project. They are the tangible expenses directly attributable to the creation of a specific project. Accurate estimation and management of these costs are paramount for bidding competitively, managing profitability, and avoiding costly overruns. Ignoring or miscalculating direct costs can lead to project failures, strained client relationships, and significant financial losses. This impacts not only individual projects but also the overall health and sustainability of construction firms. Understanding and controlling direct costs are critical for successful business operation within the competitive construction landscape. The ability to accurately predict and manage these costs often differentiates successful contractors from those struggling to maintain profitability.
Overview: What This Article Covers
This article provides a comprehensive exploration of direct costs in construction. We will delve into their definition, categories, methods of calculation, common challenges in estimation, and strategies for effective management. Readers will gain actionable insights, backed by real-world examples and best practices, empowering them to navigate the complexities of construction budgeting with confidence.
The Research and Effort Behind the Insights
This article is the result of extensive research, drawing upon industry standards, established accounting principles, case studies from successful construction projects, and input from experienced construction professionals. The information presented is intended to provide readers with accurate and reliable guidance in understanding and managing direct costs.
Key Takeaways:
- Definition and Core Concepts: A precise definition of direct costs and their key differentiating characteristics.
- Categories of Direct Costs: A detailed breakdown of the main categories of direct costs encountered in construction projects.
- Calculation Methods: Practical approaches for accurately calculating direct costs.
- Challenges in Estimation: Common pitfalls to avoid and strategies for improving accuracy.
- Management Strategies: Proven techniques for effective control and management of direct costs throughout the project lifecycle.
- Impact on Project Profitability: A clear illustration of how accurate direct cost management directly impacts a project's bottom line.
Smooth Transition to the Core Discussion
Having established the importance of understanding direct costs, let's now delve into the specifics, exploring each component in detail and providing practical strategies for effective management.
Exploring the Key Aspects of Direct Costs in Construction
1. Definition and Core Concepts:
Direct costs are expenses directly linked to the production of a specific construction project. Unlike indirect costs (overhead, administrative expenses), direct costs are readily traceable to individual projects. This traceability is essential for accurate cost accounting and project profitability analysis. A key characteristic is that these costs would not exist if the project did not.
2. Categories of Direct Costs:
Direct costs encompass several key categories:
-
Materials: This includes all raw materials, components, and supplies directly used in the construction process. Examples include lumber, concrete, steel, bricks, roofing materials, insulation, fixtures, and finishes. Accurate material take-offs and cost estimation are vital in this area.
-
Labor: This constitutes the wages, benefits, and other compensation paid to all personnel directly involved in the construction activities. This includes skilled tradespeople (carpenters, electricians, plumbers), laborers, and project supervisors working on-site.
-
Equipment: Costs associated with the use of machinery and equipment specifically employed on the project. This may include rental fees, fuel, maintenance, and operator costs for items such as excavators, cranes, bulldozers, concrete mixers, and other specialized equipment. This often includes both ownership and rental costs.
-
Subcontractor Costs: Payments made to specialized subcontractors for specific tasks or portions of the project. Examples include electrical work, plumbing, HVAC installation, and specialized finishes. These costs are direct as they are directly tied to a specific project deliverable.
3. Calculation Methods:
Accurate calculation of direct costs relies on several methods:
-
Detailed Estimates: Thorough analysis of project plans and specifications to quantify the exact quantities of materials, labor hours, and equipment needed. This involves detailed take-offs and careful consideration of potential variations.
-
Unit Costing: Assigning a unit cost (per square foot, per linear foot, etc.) to specific elements of the project. This is useful for larger projects where detailed estimations might be impractical.
-
Historical Data: Utilizing past project data to estimate costs for similar tasks and materials. However, careful consideration of inflation, market fluctuations, and project-specific variations is essential.
4. Challenges in Estimation:
Several factors can complicate accurate estimation of direct costs:
-
Unforeseen Site Conditions: Unexpected issues encountered during excavation or construction can significantly increase material and labor costs.
-
Material Price Fluctuations: Changes in commodity prices can impact the overall cost of materials. Careful monitoring of market trends is critical.
-
Labor Shortages: Difficulties in finding skilled labor can lead to delays and increased labor costs.
-
Changes in Scope: Project alterations requested by the client can necessitate revisions to the cost estimate. Clear change order processes are crucial.
5. Management Strategies:
Effective management of direct costs involves:
-
Value Engineering: Analyzing project plans to identify opportunities to reduce costs without compromising quality or functionality.
-
Careful Procurement: Strategic sourcing of materials and subcontractors to secure competitive pricing and reliable delivery.
-
Project Scheduling: Efficient scheduling of tasks to minimize delays and optimize resource utilization.
-
Cost Tracking and Control: Regular monitoring of actual costs against the budget to identify and address potential overruns promptly.
6. Impact on Project Profitability:
Accurate direct cost management is directly linked to project profitability. Underestimating direct costs can lead to losses, while overestimating can make a project uncompetitive. Effective cost control is crucial for maintaining healthy profit margins.
Exploring the Connection Between Material Procurement and Direct Costs
Effective material procurement is inextricably linked to managing direct costs. The relationship is crucial because materials often represent a substantial portion of overall project expenses. Poor procurement practices can result in significant cost overruns, delays, and quality issues.
Key Factors to Consider:
Roles and Real-World Examples: The purchasing manager plays a vital role in securing materials at optimal prices. A real-world example might involve leveraging bulk purchasing discounts or exploring alternative materials that maintain quality while reducing costs. For example, substituting standard concrete with a high-performance mix might reduce the overall quantity needed.
Risks and Mitigations: Risks include material price volatility, supply chain disruptions, and quality issues. Mitigation strategies include hedging against price fluctuations, securing multiple supply sources, and implementing robust quality control measures.
Impact and Implications: Poor material procurement can lead to cost overruns, delays, and disputes with clients. Effective procurement practices directly contribute to on-time and on-budget project completion.
Conclusion: Reinforcing the Connection
The interplay between material procurement and direct costs is pivotal to project success. By implementing efficient procurement strategies, construction firms can effectively control costs, mitigate risks, and improve overall project profitability.
Further Analysis: Examining Labor Management in Greater Detail
Labor represents another significant component of direct costs. Effective labor management significantly influences overall project cost and scheduling. Factors such as labor productivity, skill levels, and wage rates heavily impact expenses.
FAQ Section: Answering Common Questions About Direct Costs
What is the difference between direct and indirect costs?
Direct costs are directly attributable to a specific project, while indirect costs (overhead) are general business expenses shared across multiple projects.
How can I improve the accuracy of my direct cost estimates?
Use detailed take-offs, unit costing, historical data, and factor in potential contingencies.
What are some common causes of direct cost overruns?
Unforeseen site conditions, material price fluctuations, changes in scope, and inaccurate initial estimates.
How can I effectively manage direct costs during a project?
Implement robust cost tracking systems, regularly monitor progress, and use value engineering techniques.
Practical Tips: Maximizing the Benefits of Effective Direct Cost Management
- Develop a Detailed Budget: Begin with a thorough understanding of all potential direct costs.
- Track Costs Regularly: Implement a robust cost tracking system to monitor progress.
- Utilize Value Engineering: Identify cost-saving opportunities without compromising quality.
- Secure Competitive Bidding: Obtain multiple bids from subcontractors and suppliers.
- Plan for Contingencies: Allocate a percentage of the budget to account for unforeseen issues.
Final Conclusion: Wrapping Up with Lasting Insights
Understanding and managing direct costs is paramount for success in the construction industry. By diligently planning, tracking, and controlling these expenses, construction firms can enhance profitability, maintain client satisfaction, and achieve sustainable growth. Mastering direct cost management is not merely a financial exercise; it is a foundational element of responsible and successful project execution.
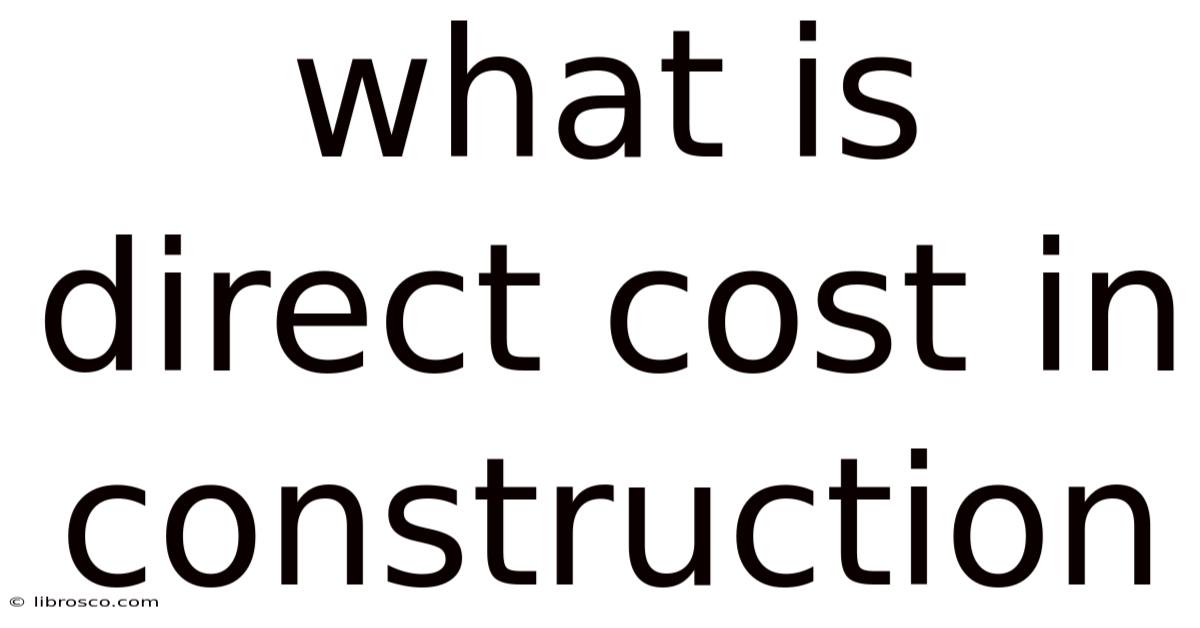
Thank you for visiting our website wich cover about What Is Direct Cost In Construction. We hope the information provided has been useful to you. Feel free to contact us if you have any questions or need further assistance. See you next time and dont miss to bookmark.
Also read the following articles
Article Title | Date |
---|---|
Childrens Term Rider Until What Age | Apr 27, 2025 |
How To Withdraw Money From Chase Investment Account To Bank Account | Apr 27, 2025 |
How Must A Replacing Producer Respond To An Applicant Wishing To Replace Existing Life | Apr 27, 2025 |
Long Term Loan Adalah | Apr 27, 2025 |
What Is Separation Theorem | Apr 27, 2025 |