What Is Direct Cost Example
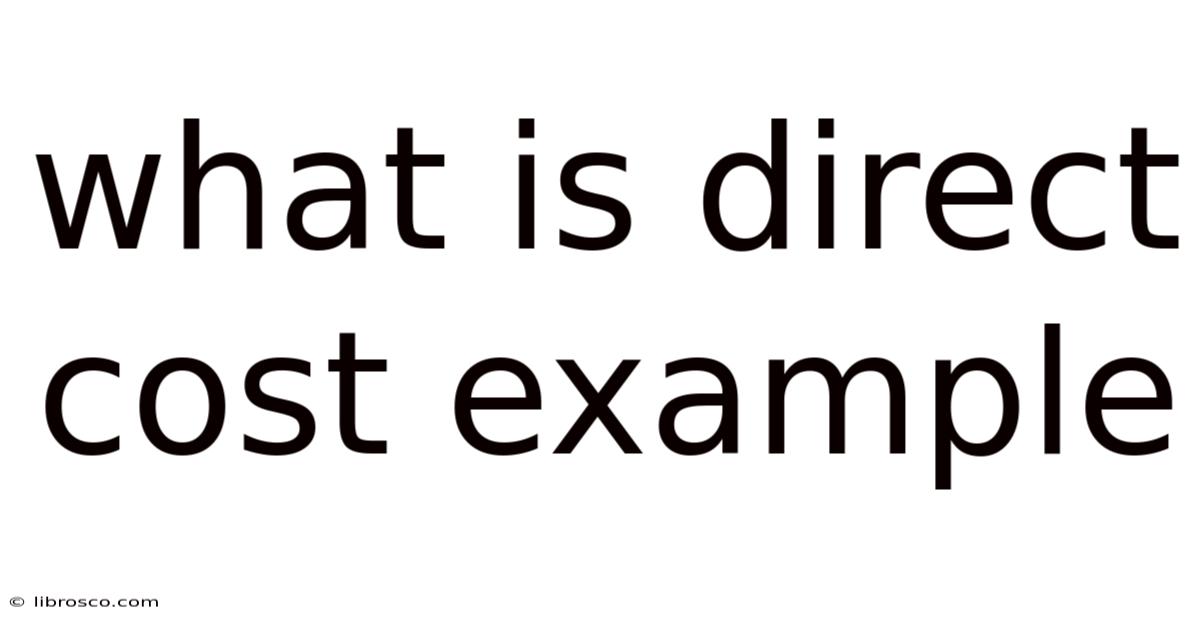
Discover more detailed and exciting information on our website. Click the link below to start your adventure: Visit Best Website meltwatermedia.ca. Don't miss out!
Table of Contents
What are the hidden secrets to accurately calculating your business's profitability? Understanding Direct Costs is Key!
Mastering direct cost calculation is the cornerstone of accurate financial reporting and strategic decision-making.
Editor’s Note: This article on direct cost examples provides a comprehensive understanding of identifying and calculating direct costs, crucial for businesses of all sizes seeking improved profitability and informed financial planning. Updated [Date of Publication].
Why Understanding Direct Costs Matters:
Profitability hinges on accurately determining a company's costs. Direct costs, those directly attributable to producing goods or services, are fundamentally important for pricing strategies, budgeting, and overall financial health. Miscalculating direct costs leads to inaccurate pricing, flawed cost-benefit analyses, and ultimately, poor decision-making. Understanding direct costs allows for better cost control, enhanced profitability, and informed strategic planning. This knowledge is critical for businesses looking to optimize operations, improve efficiency, and gain a competitive edge.
Overview: What This Article Covers
This in-depth exploration of direct costs will cover the core definition, providing numerous examples across various industries. We will delve into methods for accurate calculation, address common challenges encountered in identifying direct costs, and explore the crucial role they play in various business functions, such as pricing, budgeting, and performance evaluation. The article concludes with practical tips for effectively managing direct costs and frequently asked questions to solidify understanding.
The Research and Effort Behind the Insights
This article is the result of extensive research, drawing upon accounting principles, industry best practices, and numerous case studies. Information presented is supported by credible sources, ensuring accuracy and reliability. The structured approach provides readers with clear, actionable insights applicable to various business contexts.
Key Takeaways:
- Definition and Core Concepts: A clear explanation of direct costs and their distinction from indirect costs.
- Diverse Examples Across Industries: Real-world illustrations from manufacturing, services, and retail sectors.
- Methods for Accurate Calculation: Step-by-step guidance on calculating direct costs effectively.
- Challenges in Direct Cost Identification: Common pitfalls and strategies for overcoming them.
- Impact on Business Functions: The role of direct costs in pricing, budgeting, and performance evaluation.
- Practical Tips for Management: Actionable strategies for controlling and optimizing direct costs.
Smooth Transition to the Core Discussion:
With a foundational understanding of the significance of direct costs, let's delve into their core definition and explore numerous examples to solidify comprehension.
Exploring the Key Aspects of Direct Costs:
Definition and Core Concepts:
Direct costs are those expenses directly tied to the creation or delivery of a specific product or service. They are directly traceable to a cost object – whether that's a product, a project, or a service. This traceability is the key differentiator between direct and indirect costs. Unlike indirect costs (overhead), direct costs can be easily and accurately assigned to a specific cost object.
Diverse Examples Across Industries:
The nature of direct costs varies across industries. Let's examine examples across different sectors:
-
Manufacturing: Raw materials (wood for furniture, steel for automobiles), direct labor (wages of assembly line workers), and manufacturing supplies (lubricants, adhesives). For instance, the cost of the leather used to make a handbag is a direct cost. The wages paid to the seamstress who sews the handbag are also direct costs.
-
Services: For a consulting firm, direct costs might include the consultant's salary for the hours spent on a specific project, travel expenses directly related to that project, and any specialized software licenses used solely for that project. A lawyer's direct costs could include paralegal fees dedicated to a case and the cost of expert witnesses.
-
Retail: The cost of goods purchased for resale is a direct cost. For an online retailer, packaging materials directly used to ship a product are direct costs. A bookstore's direct cost for a specific book would be the amount paid to the publisher for that book.
-
Food Service: Direct costs for a restaurant include the cost of ingredients used to make dishes, wages of cooks and waitstaff directly involved in food preparation and service, and packaging for takeaway orders.
Methods for Accurate Calculation:
Accurately calculating direct costs requires a systematic approach:
-
Identify Cost Objects: Clearly define the products, services, or projects for which costs are being calculated.
-
Traceable Costs: Identify all costs directly related to producing or delivering the cost object. This often involves meticulous record-keeping and robust inventory management.
-
Cost Allocation: Assign the identified costs to the respective cost objects. This may involve using cost accounting methods such as job-order costing or process costing.
-
Regular Review: Regularly review cost allocation methods to ensure accuracy and adjust as needed to reflect changes in production processes or pricing strategies.
Challenges in Direct Cost Identification:
While seemingly straightforward, identifying direct costs can be challenging:
-
Joint Products: When a single process produces multiple products, allocating direct costs accurately can be complex.
-
Byproducts: The disposal or sale of byproducts can introduce complexities in direct cost calculation.
-
Indirect Costs Infiltration: Overhead costs can inadvertently become intertwined with direct costs, necessitating careful segregation.
-
Inaccurate Record-Keeping: Poor record-keeping can lead to inaccurate cost allocation and flawed financial reporting.
Overcoming these challenges involves robust inventory management systems, accurate cost tracking mechanisms, and clearly defined accounting procedures.
Impact on Business Functions:
Accurate direct cost calculation is crucial for several key business functions:
-
Pricing Strategies: Direct costs form the foundation for determining the minimum price required to achieve profitability. Understanding direct costs allows businesses to set prices competitively while ensuring sufficient profit margins.
-
Budgeting: Accurate direct cost projections are essential for creating realistic budgets and forecasting future financial performance. This enables proactive resource allocation and strategic planning.
-
Performance Evaluation: Tracking direct costs helps evaluate the efficiency and profitability of various production processes or service offerings. This allows for identification of areas for improvement and cost optimization.
-
Cost-Benefit Analysis: Direct costs are crucial input for cost-benefit analyses, informing decisions regarding investments, new product launches, and expansion strategies.
Closing Insights: Summarizing the Core Discussion
Direct costs are more than just accounting entries; they are the lifeblood of a business's financial health. Accurately identifying and managing direct costs is fundamental for effective pricing, realistic budgeting, and informed decision-making. The challenges in accurate allocation highlight the importance of meticulous record-keeping and robust cost accounting procedures.
Exploring the Connection Between Inventory Management and Direct Costs:
Efficient inventory management is inextricably linked to accurate direct cost calculation. Poor inventory management leads to inaccurate cost tracking, potentially inflating direct costs or obscuring true production costs. Let's explore this connection:
Key Factors to Consider:
-
Roles and Real-World Examples: Accurate inventory tracking ensures that raw materials, work-in-progress, and finished goods are correctly accounted for, directly impacting the calculation of direct materials costs. For example, a manufacturing company with poor inventory control might overestimate the cost of raw materials used in production, leading to artificially inflated direct costs.
-
Risks and Mitigations: Overstocking raw materials leads to increased storage costs, while understocking results in production delays and potential lost sales, indirectly impacting direct costs through lost opportunities. Effective inventory management systems, such as Just-in-Time (JIT) inventory, mitigate these risks.
-
Impact and Implications: Accurate inventory management contributes to more precise direct cost calculations, enabling businesses to set accurate pricing, make informed budget decisions, and gain a competitive advantage.
Conclusion: Reinforcing the Connection
The relationship between inventory management and direct costs is symbiotic. Robust inventory management is a prerequisite for accurate direct cost calculation, enabling efficient production, precise pricing, and optimal resource allocation. Neglecting this relationship can lead to significant financial inaccuracies and hinder business success.
Further Analysis: Examining Inventory Management Methods in Greater Detail:
Various inventory management methods influence the accuracy of direct cost calculation. Let's examine some key techniques:
-
First-In, First-Out (FIFO): This method assumes that the oldest inventory items are sold first, impacting cost of goods sold and direct cost calculations based on the cost of those oldest items.
-
Last-In, First-Out (LIFO): LIFO assumes the newest items are sold first, potentially impacting direct cost calculations differently depending on fluctuating input prices.
-
Weighted-Average Cost: This method calculates an average cost for inventory items, simplifying cost calculations but potentially lacking the precision of FIFO or LIFO.
The choice of inventory management method influences the precision of direct cost calculations, highlighting the importance of selecting a method suitable for the business and its industry.
FAQ Section: Answering Common Questions About Direct Costs:
Q: What is the difference between direct costs and indirect costs?
A: Direct costs are directly traceable to a specific product or service, while indirect costs (overhead) are shared across multiple products or services and are more difficult to allocate directly.
Q: How do I allocate direct costs to a product if I produce multiple products using the same resources?
A: This requires a more sophisticated cost allocation method, such as activity-based costing (ABC), which assigns costs based on the specific activities involved in production.
Q: Can direct labor costs include the salary of a supervisor?
A: Generally, no. While a supervisor is involved in the production process, their salary is typically considered an indirect cost (overhead), allocated across multiple production units.
Q: What happens if direct costs are miscalculated?
A: Miscalculated direct costs can lead to inaccurate pricing, flawed budgeting, incorrect performance evaluations, and poor strategic decisions, potentially impacting profitability and overall business success.
Practical Tips: Maximizing the Benefits of Accurate Direct Cost Calculation:
-
Implement Robust Inventory Management: Utilize accurate inventory tracking systems to minimize discrepancies and ensure accurate cost allocation.
-
Establish Clear Cost Accounting Procedures: Implement well-defined processes for identifying, tracking, and allocating direct costs.
-
Regularly Review and Update Cost Data: Ensure that cost data accurately reflects current production processes, material prices, and labor rates.
-
Invest in Cost Accounting Software: Leverage technology to automate cost tracking and streamline the cost allocation process.
Final Conclusion: Wrapping Up with Lasting Insights
Understanding and accurately calculating direct costs is an essential skill for any business aiming for sustained success. By implementing effective inventory management, adopting robust cost accounting procedures, and leveraging technology, businesses can gain a clear understanding of their production costs, leading to more informed decision-making, improved profitability, and a stronger competitive position in the marketplace. Mastering direct cost calculation is not merely an accounting practice; it's a strategic imperative for business success.
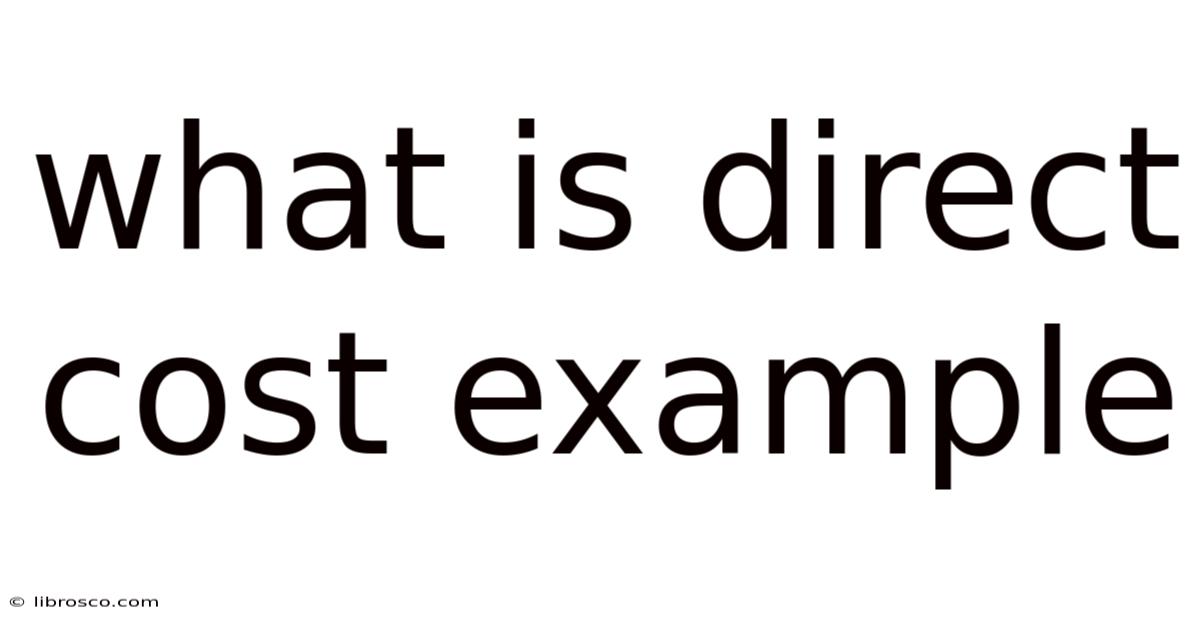
Thank you for visiting our website wich cover about What Is Direct Cost Example. We hope the information provided has been useful to you. Feel free to contact us if you have any questions or need further assistance. See you next time and dont miss to bookmark.
Also read the following articles
Article Title | Date |
---|---|
Health Insurance California Kaiser | Apr 27, 2025 |
Loan Constant Calculator Excel | Apr 27, 2025 |
Management Overlay Adjustment | Apr 27, 2025 |
How To Withdraw Money From Indodax | Apr 27, 2025 |
Is There A Difference Between Life Insurance And Life Assurance | Apr 27, 2025 |