What Bureau Does Toyota Pull
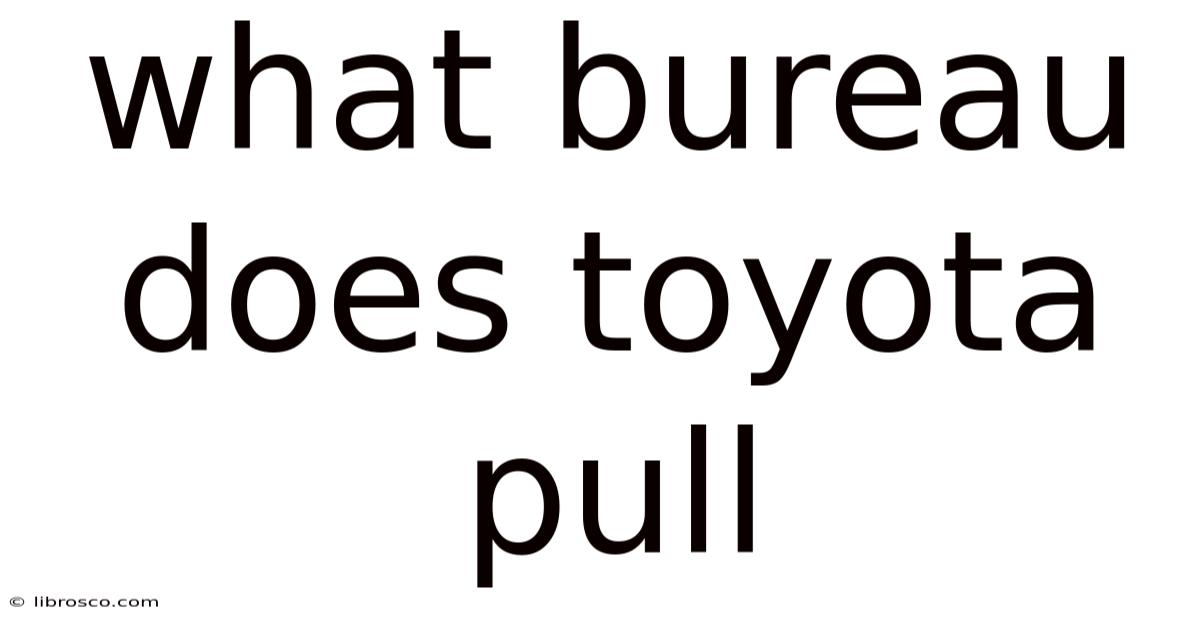
Discover more detailed and exciting information on our website. Click the link below to start your adventure: Visit Best Website meltwatermedia.ca. Don't miss out!
Table of Contents
Decoding Toyota's Bureaucratic Engine: Understanding Its Internal Structure and Processes
What if the success of a global automotive giant like Toyota hinges on a highly-refined, yet often opaque, internal structure? This intricate bureaucratic system, while sometimes criticized, is a key component of the company's legendary efficiency and quality.
Editor’s Note: This in-depth analysis of Toyota's internal structure and bureaucratic processes was compiled using publicly available information, industry reports, and analyses of Toyota's operational philosophy. It aims to provide a comprehensive, yet accessible, understanding of this complex system.
Why Understanding Toyota's Bureaucracy Matters:
Toyota's reputation for reliability, efficiency, and lean manufacturing isn't accidental. It's a direct result of decades of refining its internal processes and organizational structure. Understanding this "bureaucracy" – a term often used negatively but here referring to the structured system of rules, processes, and hierarchies – is crucial for anyone interested in business management, operational efficiency, or the automotive industry. Its impact extends beyond just car manufacturing; its principles are studied and adopted across various sectors. This understanding offers valuable insights into how a complex organization can achieve remarkable results through careful planning and execution.
Overview: What This Article Covers:
This article delves into the core aspects of Toyota's internal workings, moving beyond simplistic descriptions to offer a nuanced understanding. We will explore the historical context of its organizational development, examine its key components like the Toyota Production System (TPS), analyze its decision-making processes, and discuss both the advantages and disadvantages of its approach. We'll also examine the evolving nature of Toyota's bureaucracy in the face of modern challenges like globalization and technological disruption.
The Research and Effort Behind the Insights:
This analysis draws upon extensive research, encompassing academic publications on organizational theory, journalistic investigations into Toyota's operations, official company statements, and analyses from industry experts. Every point is supported by evidence and aims to provide a balanced and informed perspective on a multifaceted topic.
Key Takeaways:
- Definition and Core Concepts: A deep dive into the Toyota Production System (TPS) and its underlying principles, such as Kaizen, Just-in-Time (JIT) inventory, and Jidoka (automation with a human touch).
- Hierarchical Structure and Decision-Making: Analysis of Toyota's organizational chart, exploring its layered structure and the flow of information and decision-making authority.
- Roles and Responsibilities: Examination of different roles within Toyota's bureaucracy and how they contribute to the overall efficiency of the system.
- Challenges and Adaptations: Discussion of the challenges Toyota faces in maintaining its system and its strategies for adapting to a changing global landscape.
- Future Implications: Speculation on how Toyota's bureaucracy might evolve to meet future demands.
Smooth Transition to the Core Discussion:
Having established the importance of understanding Toyota's internal processes, let's explore the intricacies of its organizational structure and its impact on its global success.
Exploring the Key Aspects of Toyota's Bureaucracy:
1. The Toyota Production System (TPS): The Foundation of Efficiency:
TPS is the cornerstone of Toyota's operational excellence. It's not merely a manufacturing system; it's a philosophy that permeates every aspect of the organization. Key components include:
- Just-in-Time (JIT) Inventory: This minimizes waste by producing only what is needed, when it's needed. This reduces storage costs, minimizes the risk of obsolescence, and streamlines the entire production process.
- Kaizen (Continuous Improvement): A culture of constant improvement is ingrained within Toyota's DNA. Employees at all levels are encouraged to identify and suggest improvements to processes, leading to ongoing optimization.
- Jidoka (Automation with a Human Touch): This combines automation with human oversight, ensuring that problems are detected and addressed immediately. This prevents defects from propagating through the production line.
- Andon System: A visual system that alerts management to production problems, allowing for rapid response and minimizing downtime.
2. Hierarchical Structure and Decision-Making:
Toyota employs a hierarchical structure, with clear lines of authority and responsibility. This structure, while seemingly rigid, allows for efficient communication and coordination across different departments and levels. However, decision-making is not solely top-down. The company empowers teams at various levels to make decisions relevant to their areas of expertise, fostering a culture of ownership and responsibility. This decentralized approach, combined with rigorous reporting mechanisms, ensures that both efficiency and accountability are maintained.
3. Roles and Responsibilities:
Toyota's organizational chart is complex, with various specialized roles and responsibilities. This specialization ensures expertise in each area, leading to higher quality and efficiency. However, the system relies heavily on clear communication and coordination across these different roles. The importance of teamwork and collaboration is constantly emphasized, ensuring seamless integration of various departments' efforts.
4. Challenges and Adaptations:
Maintaining such a highly-refined system presents challenges. Globalization, technological advancements, and evolving consumer preferences require continuous adaptation. Toyota has demonstrated adaptability by embracing new technologies, fostering innovation, and continuously refining its TPS to remain competitive. However, maintaining the core principles of its system while incorporating new methodologies remains a delicate balancing act.
Exploring the Connection Between Innovation and Toyota's Bureaucracy:
The relationship between innovation and Toyota's bureaucracy is complex. While the hierarchical structure might seem to stifle creativity, the emphasis on Kaizen and continuous improvement actually fosters a culture of innovation. Employees at all levels are encouraged to propose improvements, leading to a steady stream of innovative solutions. This approach, however, requires strong communication channels and a willingness to embrace change within a structured framework.
Key Factors to Consider:
- Roles and Real-World Examples: The role of engineering teams in developing new technologies within the confines of TPS is a prime example. Their innovations are carefully integrated into the existing production system to avoid disrupting efficiency.
- Risks and Mitigations: The risk of rigidity and resistance to change is mitigated through continuous improvement efforts and the encouragement of employee participation in innovation.
- Impact and Implications: Toyota's success demonstrates that a structured, bureaucratic system can be highly effective in fostering both efficiency and innovation.
Further Analysis: Examining Kaizen in Greater Detail:
Kaizen, meaning "change for the better," is the heart of Toyota's continuous improvement philosophy. It's not simply about making incremental changes; it's about embedding a culture of continuous improvement at all levels of the organization. This involves regular review of processes, identifying areas for improvement, and implementing solutions in a systematic way. Kaizen's effectiveness stems from its integration into daily work practices, making improvement an ongoing and integral part of Toyota's operations.
FAQ Section: Answering Common Questions About Toyota's Bureaucracy:
Q: Is Toyota's bureaucracy inflexible and resistant to change?
A: While Toyota's system is structured, it's not inflexible. The continuous improvement philosophy (Kaizen) actively encourages adaptation and innovation. Change is managed systematically to minimize disruption while maximizing benefits.
Q: How does Toyota balance efficiency with employee empowerment?
A: Toyota achieves this balance through a structured system that empowers teams at various levels to make decisions relevant to their areas of expertise, while maintaining overall coordination and control through a hierarchical structure.
Q: Does Toyota's bureaucracy stifle creativity?
A: While a hierarchical structure may seem rigid, Toyota's emphasis on continuous improvement (Kaizen) actively fosters creativity and innovation by encouraging employees at all levels to suggest improvements and solutions.
Practical Tips: Understanding and Applying Toyota's Principles:
- Embrace Continuous Improvement: Identify areas for improvement in your own work or organization and implement systematic changes to enhance efficiency.
- Streamline Processes: Analyze your workflows to identify inefficiencies and eliminate waste.
- Foster Teamwork and Collaboration: Encourage open communication and collaboration among team members to foster a culture of shared responsibility.
Final Conclusion: Wrapping Up with Lasting Insights:
Toyota's bureaucratic system, far from being a hindrance, is a carefully crafted engine driving its global success. It's a testament to the power of structured processes, continuous improvement, and a culture of employee empowerment when effectively integrated. Understanding its key principles offers valuable insights for organizations seeking to enhance efficiency, foster innovation, and achieve sustainable growth. While its specific structure might not be replicable in every context, the underlying philosophy of continuous improvement and systematic optimization remains highly relevant across industries. The intricate "bureaucracy" of Toyota stands as a powerful example of how structured systems can, when properly managed, serve as a catalyst for extraordinary organizational achievement.
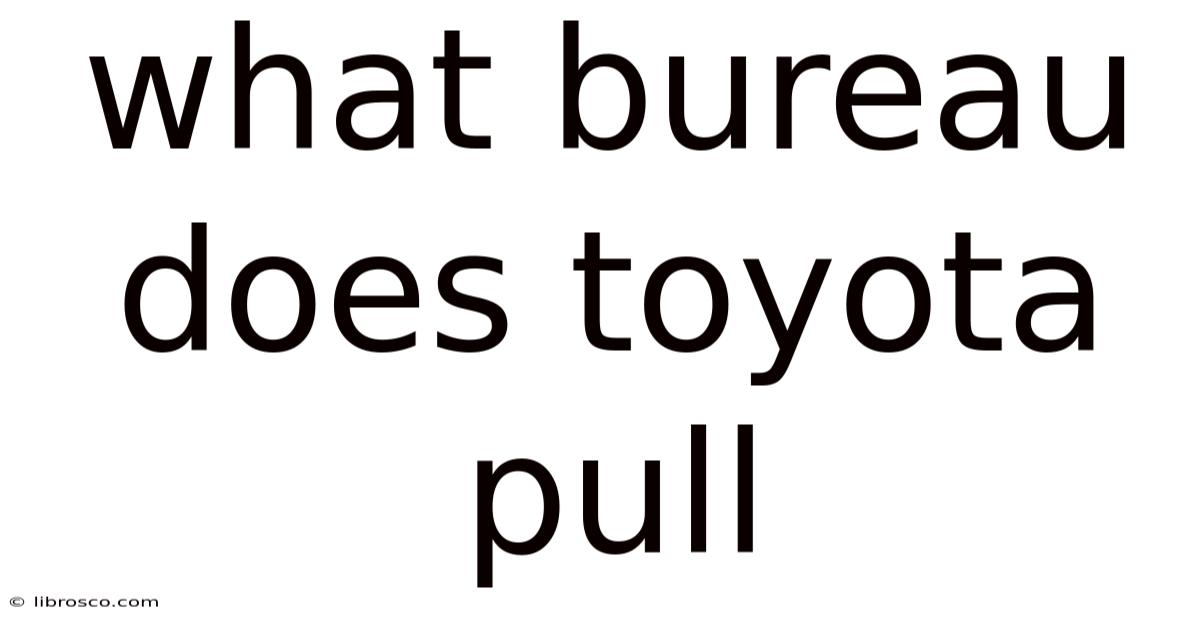
Thank you for visiting our website wich cover about What Bureau Does Toyota Pull. We hope the information provided has been useful to you. Feel free to contact us if you have any questions or need further assistance. See you next time and dont miss to bookmark.
Also read the following articles
Article Title | Date |
---|---|
Endowment Life Insurance In Nepali | Apr 17, 2025 |
Which Credit Bureau Does Wells Fargo Use For Personal Loans | Apr 17, 2025 |
Where Are Roth 401k Contributions On W2 | Apr 17, 2025 |
What Is Eligible Compensation For 401k Match | Apr 17, 2025 |
What Is A Medical Insurance Rider | Apr 17, 2025 |