What Are Workplace Controls
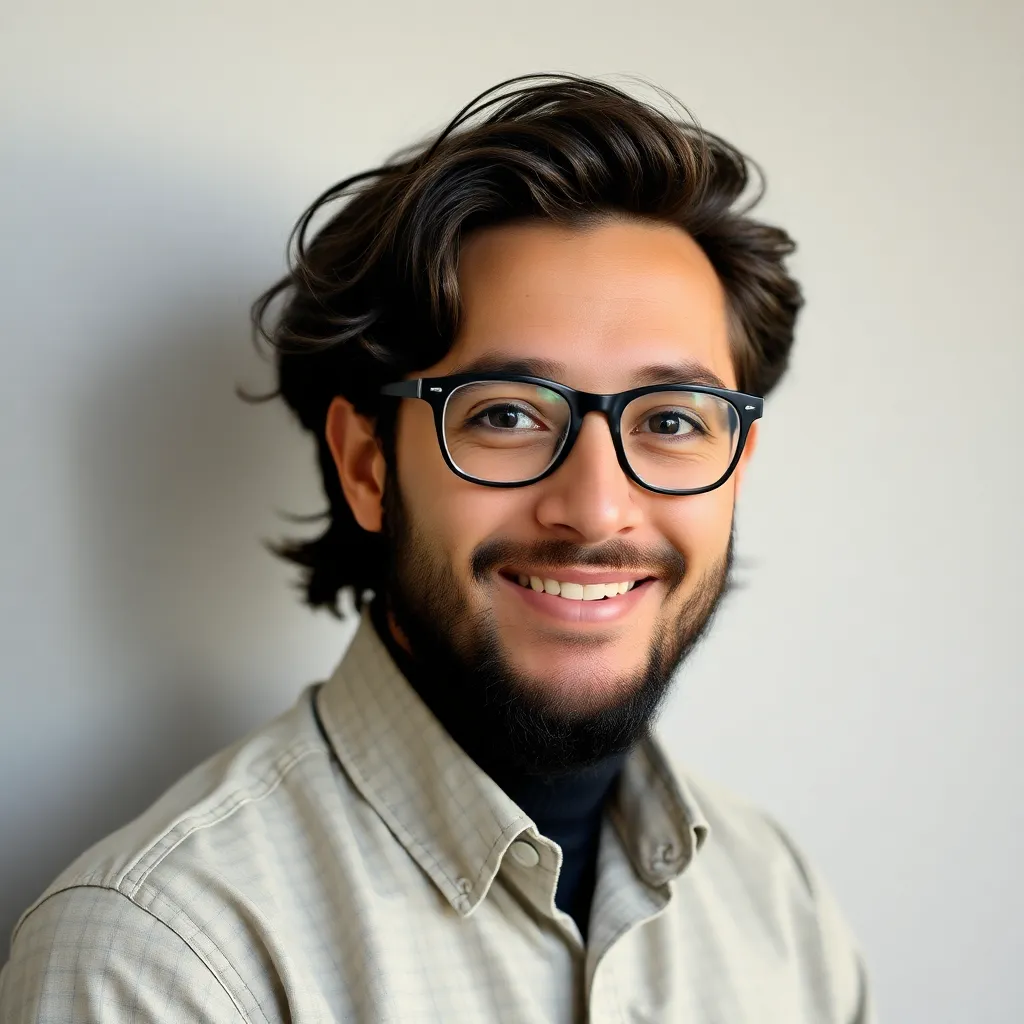
adminse
Apr 01, 2025 · 9 min read

Table of Contents
Unveiling the Power of Workplace Controls: A Comprehensive Guide
What if workplace safety and productivity hinged on a deeper understanding of workplace controls? This multifaceted approach is crucial for creating thriving and secure work environments.
Editor’s Note: This article on workplace controls was published today, providing you with the latest insights and best practices to ensure a safe and productive workplace.
Why Workplace Controls Matter: Relevance, Practical Applications, and Industry Significance
Workplace controls represent a cornerstone of occupational safety and health (OSH). They are the systematic measures implemented to eliminate or minimize hazards, safeguarding employees from workplace risks and fostering a culture of safety. The significance of effective workplace controls extends beyond simply complying with regulations; they are vital for boosting productivity, reducing worker compensation claims, enhancing employee morale, and improving a company's overall reputation. From manufacturing plants to office spaces, healthcare facilities to construction sites, the application of appropriate controls is paramount across diverse industries. Failure to implement adequate controls can lead to costly accidents, injuries, illnesses, and even fatalities, resulting in significant financial burdens and legal repercussions.
Overview: What This Article Covers
This article provides a comprehensive exploration of workplace controls. We will delve into the various types of controls, examining their applications, limitations, and the hierarchy of control measures. Furthermore, we will analyze the critical role of risk assessment in selecting appropriate controls and discuss the importance of ongoing monitoring and evaluation to ensure their continued effectiveness. Readers will gain a practical understanding of how to implement and manage workplace controls, thereby contributing to a safer and more productive work environment.
The Research and Effort Behind the Insights
This article is the result of extensive research, drawing upon established OSH standards, best practices from various industries, and relevant case studies. We have consulted authoritative sources, including the Occupational Safety and Health Administration (OSHA) guidelines, the National Institute for Occupational Safety and Health (NIOSH) recommendations, and numerous peer-reviewed publications to ensure accuracy and validity. The information presented is intended to be comprehensive and practical, offering actionable insights for businesses and safety professionals.
Key Takeaways:
- Definition and Core Concepts: A clear explanation of workplace controls and their underlying principles.
- Types of Controls: A detailed breakdown of the hierarchy of controls, including elimination, substitution, engineering controls, administrative controls, and personal protective equipment (PPE).
- Risk Assessment and Control Selection: The vital role of risk assessment in determining the appropriate control measures for specific hazards.
- Implementation and Management: Practical steps for implementing and maintaining effective workplace controls.
- Monitoring and Evaluation: Strategies for ongoing monitoring and evaluation to ensure control effectiveness.
- Legal and Regulatory Compliance: Understanding relevant OSH regulations and standards.
Smooth Transition to the Core Discussion
Having established the importance of workplace controls, let's now delve into the specifics, examining each type of control and its application within the broader framework of risk management.
Exploring the Key Aspects of Workplace Controls
1. Definition and Core Concepts:
Workplace controls encompass a range of measures designed to prevent or minimize exposure to workplace hazards. These hazards can be physical (noise, radiation, heat), chemical (toxic substances, fumes), biological (bacteria, viruses), ergonomic (repetitive movements, awkward postures), or psychosocial (stress, harassment). The aim is to proactively manage risks, creating a work environment where employees can perform their tasks safely and effectively.
2. Types of Controls: The Hierarchy of Controls
The hierarchy of controls is a fundamental principle in OSH, outlining a prioritized approach to hazard management. It emphasizes the most effective and preferred methods first, progressing to less effective options only when others are infeasible. This hierarchy is typically represented as follows:
-
Elimination: This is the most effective control measure, involving the complete removal of the hazard. For example, eliminating a hazardous process altogether or redesigning a workflow to remove the need for a hazardous substance.
-
Substitution: This involves replacing a hazardous substance or process with a less hazardous alternative. For example, replacing a toxic solvent with a less toxic one or using automated equipment to reduce manual handling.
-
Engineering Controls: These controls isolate people from the hazard. Examples include machine guarding, ventilation systems, enclosed workspaces, and the use of robotic systems to handle hazardous materials. They are often implemented as a permanent solution.
-
Administrative Controls: These controls change the way work is done, managing the exposure of workers to hazards. Examples include job rotation, limiting exposure time, providing adequate training and supervision, and implementing safe work procedures. These controls often involve changes to work practices, scheduling, or training programs.
-
Personal Protective Equipment (PPE): PPE is the last line of defense, providing personal protection against hazards. This includes items such as safety glasses, respirators, gloves, hearing protection, and safety footwear. While essential, PPE should only be used when other controls are not feasible or sufficient. It is important to note that PPE only protects the individual wearing it and does not address the hazard itself.
3. Risk Assessment and Control Selection:
Risk assessment is the foundation for selecting appropriate workplace controls. It involves identifying hazards, assessing the risks associated with those hazards, and determining the necessary control measures to mitigate those risks. A thorough risk assessment considers the likelihood of an incident occurring and the potential severity of its consequences. The outcome guides the selection of appropriate control measures from the hierarchy, starting with elimination and substitution and progressing to other methods as needed.
4. Implementation and Management:
Implementing workplace controls involves a multi-step process:
- Planning: Develop a comprehensive plan that outlines the chosen controls, responsibilities, timelines, and resources required.
- Procurement: Purchase or lease the necessary equipment, materials, and software.
- Installation: Install and configure the controls according to manufacturers' specifications and OSH best practices.
- Training: Provide comprehensive training to employees on the proper use and maintenance of the controls.
- Documentation: Maintain detailed records of the risk assessments, control measures implemented, training provided, and any incidents or near misses.
5. Monitoring and Evaluation:
Ongoing monitoring and evaluation are critical to ensure the continued effectiveness of workplace controls. Regular inspections, audits, and reviews should be conducted to identify any deficiencies or areas for improvement. Data collection and analysis can help track the effectiveness of controls, identify trends, and refine strategies for hazard management.
6. Legal and Regulatory Compliance:
Businesses must comply with relevant OSH legislation and regulations. This involves implementing the necessary controls to meet the requirements set forth by regulatory bodies. Failure to comply can lead to fines, legal action, and damage to a company’s reputation.
Exploring the Connection Between Training and Workplace Controls
The relationship between training and workplace controls is undeniably pivotal. Effective workplace controls are useless without the knowledge and understanding of how to use them safely and correctly. Training plays a crucial role in bridging this gap, ensuring employees understand the hazards they face, the controls implemented to mitigate those hazards, and how to use the controls effectively.
Key Factors to Consider:
Roles and Real-World Examples: Training programs should cover the specific hazards associated with each task, the control measures in place, and the proper procedures for using those controls. For example, training on the use of machinery should include demonstrations of machine guarding, lockout/tagout procedures, and safe operating procedures. Training on chemical handling should encompass safe handling procedures, the use of PPE, and emergency response protocols.
Risks and Mitigations: Inadequate training can lead to incorrect use of controls, rendering them ineffective and increasing the risk of accidents. To mitigate this risk, training programs should be comprehensive, engaging, and regularly updated to reflect any changes in procedures or technology. They should include both theoretical knowledge and hands-on practice.
Impact and Implications: Effective training programs lead to increased safety awareness, better compliance with safety procedures, and a reduction in workplace accidents and injuries. It empowers employees to actively participate in maintaining a safe work environment.
Conclusion: Reinforcing the Connection
The interplay between training and workplace controls underscores the interconnectedness of safety and productivity. By investing in comprehensive and effective training programs, businesses can ensure their workplace controls are not only implemented but also utilized correctly, maximizing their protective capabilities.
Further Analysis: Examining Training Methods in Greater Detail
Numerous training methods exist, each with its advantages and disadvantages. These range from traditional classroom-based lectures and demonstrations to interactive simulations, online courses, and on-the-job training. The most effective approach often involves a combination of methods tailored to the specific needs of the employees and the hazards being addressed. Factors to consider include the learning styles of the employees, the complexity of the information, and the availability of resources.
FAQ Section: Answering Common Questions About Workplace Controls
What is a hazard? A hazard is anything that has the potential to cause harm. This could be a physical substance, a process, a piece of equipment, or even a work practice.
What is a risk? A risk is the likelihood of harm occurring from exposure to a hazard. It considers both the probability of the hazard causing harm and the severity of the potential harm.
How often should workplace controls be reviewed? Workplace controls should be reviewed regularly, ideally at least annually, or more frequently if there are significant changes in the workplace or if an incident occurs.
What happens if an employee doesn't follow safety procedures? Failure to follow safety procedures can lead to disciplinary action, up to and including termination of employment. More importantly, it significantly increases the risk of accidents and injuries.
What if a hazard is not listed in the risk assessment? If a hazard is not included in the initial risk assessment, a supplemental assessment should be conducted immediately to address the new hazard and implement the necessary control measures.
Practical Tips: Maximizing the Benefits of Workplace Controls
- Conduct thorough risk assessments: Regularly assess your workplace for potential hazards and update assessments as needed.
- Prioritize control measures: Implement the hierarchy of controls, starting with elimination and substitution.
- Provide comprehensive training: Equip your employees with the knowledge and skills necessary to use workplace controls effectively.
- Monitor and evaluate controls: Conduct regular inspections and audits to ensure controls remain effective.
- Document all procedures: Maintain accurate records of risk assessments, training programs, and control measures.
- Stay updated on regulations: Keep abreast of changes in OSH legislation and ensure compliance.
- Promote a safety culture: Foster a workplace where safety is a shared value and responsibility.
Final Conclusion: Wrapping Up with Lasting Insights
Workplace controls are not merely regulatory requirements; they are essential elements of a safe, productive, and thriving work environment. By implementing a robust system of controls, supported by thorough risk assessments and effective training, businesses can significantly reduce the risk of accidents, protect their employees, and foster a culture of safety. The commitment to a proactive approach to workplace safety is not just a moral obligation but a crucial investment in the well-being of employees and the success of the organization. The insights provided in this article empower stakeholders to take a proactive approach, creating a workplace where safety is paramount and productivity flourishes.
Latest Posts
Latest Posts
-
How To Pass Credit Check For Car Finance
Apr 04, 2025
-
How To Pass Credit Check For Mobile Phones
Apr 04, 2025
-
How To Pass A Rental Credit Check For Free
Apr 04, 2025
-
How To Pass A Credit Score Check
Apr 04, 2025
-
How To Pass A Rental Credit Check Reddit
Apr 04, 2025
Related Post
Thank you for visiting our website which covers about What Are Workplace Controls . We hope the information provided has been useful to you. Feel free to contact us if you have any questions or need further assistance. See you next time and don't miss to bookmark.