Obsolete Inventory Calculation
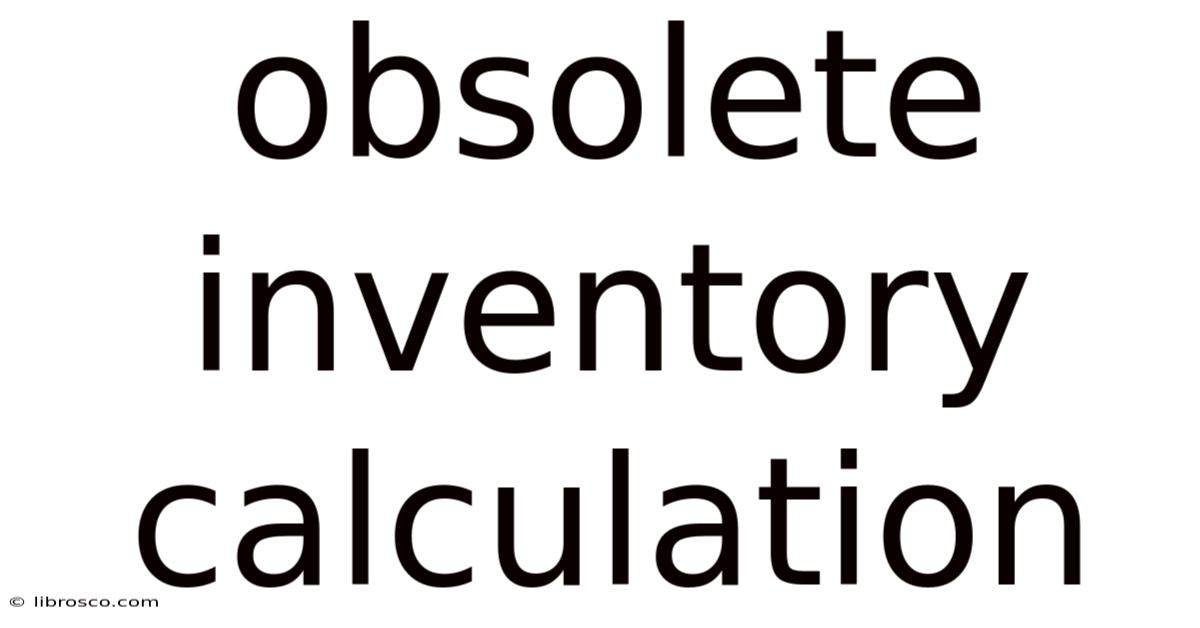
Discover more detailed and exciting information on our website. Click the link below to start your adventure: Visit Best Website meltwatermedia.ca. Don't miss out!
Table of Contents
Calculating Obsolete Inventory: A Comprehensive Guide to Identifying and Managing Dead Stock
What if the silent killer of profitability is hiding in your warehouse? Obsolete inventory, often overlooked, can significantly drain resources and hinder growth.
Editor’s Note: This comprehensive guide to obsolete inventory calculation was published today, providing you with the latest strategies and best practices for identifying and managing dead stock. This article will equip you with the tools and knowledge to effectively tackle this often-overlooked challenge and enhance your bottom line.
Why Obsolete Inventory Matters: Relevance, Practical Applications, and Industry Significance
Obsolete inventory, or dead stock, refers to items that are no longer sellable due to factors like obsolescence, damage, or changes in market demand. It's a silent drain on resources, occupying valuable warehouse space, tying up capital that could be invested elsewhere, and incurring costs associated with storage, insurance, and potential disposal. Accurate calculation of obsolete inventory is crucial for efficient inventory management, improved profitability, and maintaining a healthy cash flow. Across all industries, from retail and manufacturing to technology and healthcare, the impact of obsolete inventory is significant, directly affecting profitability, efficiency, and competitiveness.
Overview: What This Article Covers
This article provides a detailed exploration of obsolete inventory calculation methods. We will cover various techniques for identifying obsolete inventory, different calculation approaches, the importance of accurate cost accounting, strategies for mitigating obsolete inventory buildup, and best practices for minimizing losses. Readers will gain actionable insights and practical strategies to effectively manage their inventory and boost profitability.
The Research and Effort Behind the Insights
This article is the result of extensive research, drawing from industry best practices, academic literature on inventory management, and case studies of successful inventory control implementations. We have incorporated various calculation methods, highlighting their strengths and weaknesses, to provide a comprehensive overview of the topic. The goal is to equip readers with a thorough understanding of how to effectively identify and address the problem of obsolete inventory.
Key Takeaways:
- Definition and Core Concepts: A clear understanding of what constitutes obsolete inventory and its various contributing factors.
- Identification Methods: Different techniques for pinpointing obsolete items, from analyzing sales data to conducting physical inventory checks.
- Calculation Methods: Several approaches for quantifying the value of obsolete inventory, including the cost-of-goods-sold (COGS) method and the market value method.
- Cost Accounting: The importance of accurate cost allocation in obsolete inventory calculations.
- Mitigation Strategies: Proactive measures to minimize the risk of obsolete inventory buildup.
- Best Practices: Practical steps for implementing effective inventory management systems.
Smooth Transition to the Core Discussion:
With a grasp of why accurate obsolete inventory calculation is critical, let's delve into the practical aspects of identifying and quantifying this costly inventory burden.
Exploring the Key Aspects of Obsolete Inventory Calculation
1. Definition and Core Concepts:
Obsolete inventory is inventory that has lost its value due to a number of factors. These can include:
- Technological Obsolescence: Products rendered outdated by newer technologies. Think older model electronics or software.
- Changes in Consumer Demand: Shifts in market preferences leading to decreased demand for specific products. A fashion trend fading, for example.
- Damage or Deterioration: Inventory damaged during storage or transportation, or products with a limited shelf life that have expired.
- Overstocking: Holding excessive inventory beyond actual demand, leading to some items becoming obsolete before they can be sold.
- Product Lifecycle: Reaching the end of a product's lifecycle, making it unsaleable.
2. Identification Methods:
Identifying obsolete inventory requires a multi-pronged approach:
- Sales Data Analysis: Analyzing sales trends to identify slow-moving or stagnant items. A declining sales rate over a defined period is a strong indicator.
- ABC Analysis: Categorizing inventory based on its value and consumption rate. Focus efforts on managing high-value, slow-moving items (class C).
- Inventory Turnover Ratio: Calculating how quickly inventory is sold. Low turnover ratios suggest potential obsolescence.
- Physical Inventory Counts: Regularly conducting physical inventory checks to identify damaged, outdated, or misplaced items.
- Technology-Driven Solutions: Employing inventory management software with features for automatic alert generation on slow-moving items or near-expiration dates.
3. Calculation Methods:
Several methods exist for calculating the value of obsolete inventory:
-
Cost of Goods Sold (COGS) Method: This method uses the historical cost of the inventory. It's straightforward but may not accurately reflect the current market value. The formula typically involves subtracting the current market value of the inventory from its original cost.
-
Market Value Method: This method uses the current market price of the inventory, reflecting its current worth. It is more realistic than the COGS method but requires accurate market price data. It's calculated by comparing the current market value to the cost, finding the difference (which will be negative for obsolete items) and using that as the value of the obsolete inventory.
-
Net Realizable Value (NRV) Method: This method focuses on what the company can realistically get for the obsolete inventory, whether it be through liquidation, salvage, or scrap. This accounts for potential selling costs. NRV is calculated as the estimated selling price minus any estimated selling costs.
-
Reserve Method: This method involves establishing a reserve account for potential losses from obsolete inventory. The amount in the reserve account is periodically adjusted based on assessments of the inventory's obsolescence risk.
The choice of method depends on the company's accounting policies, the nature of the inventory, and the availability of data.
4. Cost Accounting’s Crucial Role:
Accurate cost accounting is crucial for any inventory calculation, including obsolescence. Accurate costing ensures that the calculation accurately reflects the true financial impact of the obsolete inventory. This includes considering all costs associated with the inventory, such as purchasing, storage, handling, and transportation. Any indirect costs that can be tied to the inventory should also be included.
5. Mitigation Strategies:
Preventing obsolete inventory buildup is far more effective than dealing with it after it has accumulated. Strategies include:
- Demand Forecasting: Accurate demand forecasting using various techniques (e.g., time series analysis, moving averages) helps optimize ordering quantities.
- Effective Inventory Management Systems: Implementing robust inventory management systems with real-time tracking and reporting capabilities.
- Just-in-Time (JIT) Inventory: Minimizing inventory holding by ordering goods only when needed.
- Vendor Managed Inventory (VMI): Allowing suppliers to manage inventory levels based on real-time demand data.
- Improved Communication and Collaboration: Strengthening communication between departments (sales, purchasing, production) to ensure accurate demand planning.
- Regular Inventory Reviews: Conducting regular reviews of slow-moving items to identify potential obsolescence early on.
6. Best Practices:
- Regular Physical Inventory Counts: Regular physical counts to validate inventory records and identify discrepancies early on.
- Effective Storage and Handling: Proper storage to prevent damage or deterioration.
- First-In, First-Out (FIFO): Employing FIFO inventory management to ensure older inventory is sold first.
- Use of Technology: Implementing inventory management software that tracks key metrics, including sales history and inventory turnover.
Closing Insights: Summarizing the Core Discussion
Accurate obsolete inventory calculation is vital for maintaining financial health and maximizing profitability. By employing the methods and strategies discussed, businesses can effectively identify, quantify, and mitigate the impact of obsolete inventory. This ultimately leads to better resource allocation, improved cash flow, and enhanced competitiveness.
Exploring the Connection Between Accurate Costing and Obsolete Inventory Calculation
Accurate costing is not simply a matter of good accounting practice; it's fundamental to effective obsolete inventory management. The connection is direct and significant. Inaccurate cost allocation leads to flawed obsolete inventory calculations, resulting in inaccurate financial reporting and poor decision-making.
Key Factors to Consider:
-
Roles and Real-World Examples: Inaccurate costing can lead to underestimating or overestimating the value of obsolete inventory. A company using a simplified costing method may not capture all the indirect costs associated with a product, leading to an underestimation of its obsolescence cost.
-
Risks and Mitigations: Underestimating obsolete inventory can hide the true extent of financial losses, hindering effective corrective actions. Overestimating can lead to unnecessary write-downs, affecting profitability. To mitigate these risks, companies should implement robust cost accounting systems and regularly review their costing methods.
-
Impact and Implications: Inaccurate obsolete inventory calculations can misrepresent a company's financial position, affecting its credit rating, investor confidence, and overall market valuation. It also impacts the accuracy of key performance indicators (KPIs).
Conclusion: Reinforcing the Connection
The link between precise costing and accurate obsolete inventory valuation is undeniable. By investing in robust cost accounting systems and continuously refining costing methods, businesses can accurately assess the financial burden of obsolete inventory, enabling informed decisions, improved inventory management, and ultimately, enhanced profitability.
Further Analysis: Examining Demand Forecasting in Greater Detail
Demand forecasting plays a crucial role in preventing obsolete inventory buildup. By accurately predicting future demand, businesses can optimize their ordering quantities, reducing the risk of overstocking. Various forecasting techniques exist, each with its strengths and weaknesses. These include moving averages, exponential smoothing, ARIMA models, and more sophisticated AI-driven forecasting methods. Choosing the right method depends on factors like data availability, forecasting horizon, and the complexity of the product's demand pattern.
FAQ Section: Answering Common Questions About Obsolete Inventory Calculation
-
What is the best method for calculating obsolete inventory? There is no single "best" method. The optimal approach depends on factors such as the nature of the inventory, the availability of data, and the company's accounting policies. Consider the COGS, Market Value, and NRV methods and select the most appropriate one.
-
How often should I review my inventory for obsolescence? Regular reviews are essential. The frequency depends on the industry and the nature of the inventory. A monthly review is recommended for fast-moving consumer goods, while a quarterly review might suffice for slower-moving items.
-
What should I do with obsolete inventory? Options include selling it at a discounted price, liquidating it through auctions or online marketplaces, donating it to charity, or recycling or disposing of it responsibly.
Practical Tips: Maximizing the Benefits of Effective Obsolete Inventory Management
- Implement an Inventory Management System: Invest in robust software to automate tracking, analysis, and reporting.
- Regularly Analyze Sales Data: Identify trends and patterns to predict potential obsolescence early.
- Perform Regular Physical Inventory Counts: Ensure accuracy of inventory records and identify damaged or misplaced goods.
- Develop a Clear Obsolescence Policy: Define criteria for identifying and handling obsolete inventory.
- Collaborate Across Departments: Encourage communication and information sharing between sales, purchasing, and warehouse teams.
Final Conclusion: Wrapping Up with Lasting Insights
Obsolete inventory is a significant challenge for businesses of all sizes. However, by understanding the various calculation methods, implementing effective mitigation strategies, and employing best practices, organizations can significantly reduce the financial burden of dead stock. Proactive inventory management is not just cost-saving; it’s a key driver of profitability and operational efficiency. By continuously monitoring inventory levels, analyzing sales data, and employing appropriate forecasting techniques, businesses can transform their inventory management from a potential liability into a strategic asset.
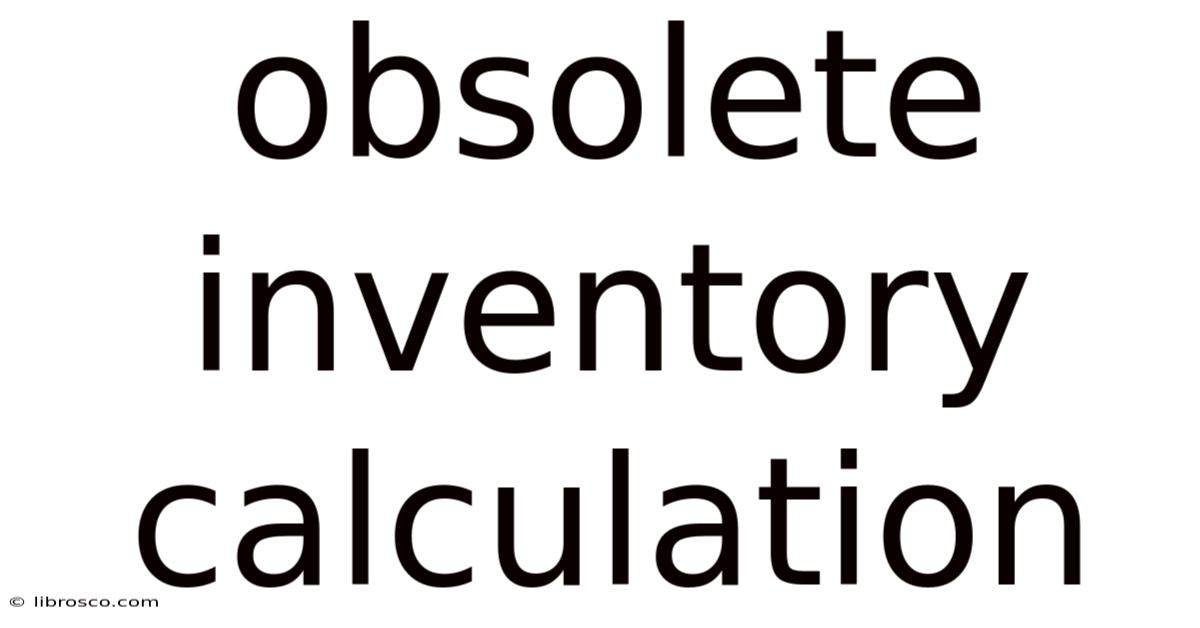
Thank you for visiting our website wich cover about Obsolete Inventory Calculation. We hope the information provided has been useful to you. Feel free to contact us if you have any questions or need further assistance. See you next time and dont miss to bookmark.
Also read the following articles
Article Title | Date |
---|---|
What Is Tax Accountant Job | Apr 21, 2025 |
What Is Tax Basis Accounting | Apr 21, 2025 |
Electronic Banking Definition | Apr 21, 2025 |
Online Banking Definition Quizlet | Apr 21, 2025 |
Mosaic Theory Meaning | Apr 21, 2025 |