Flexible Manufacturing System Example
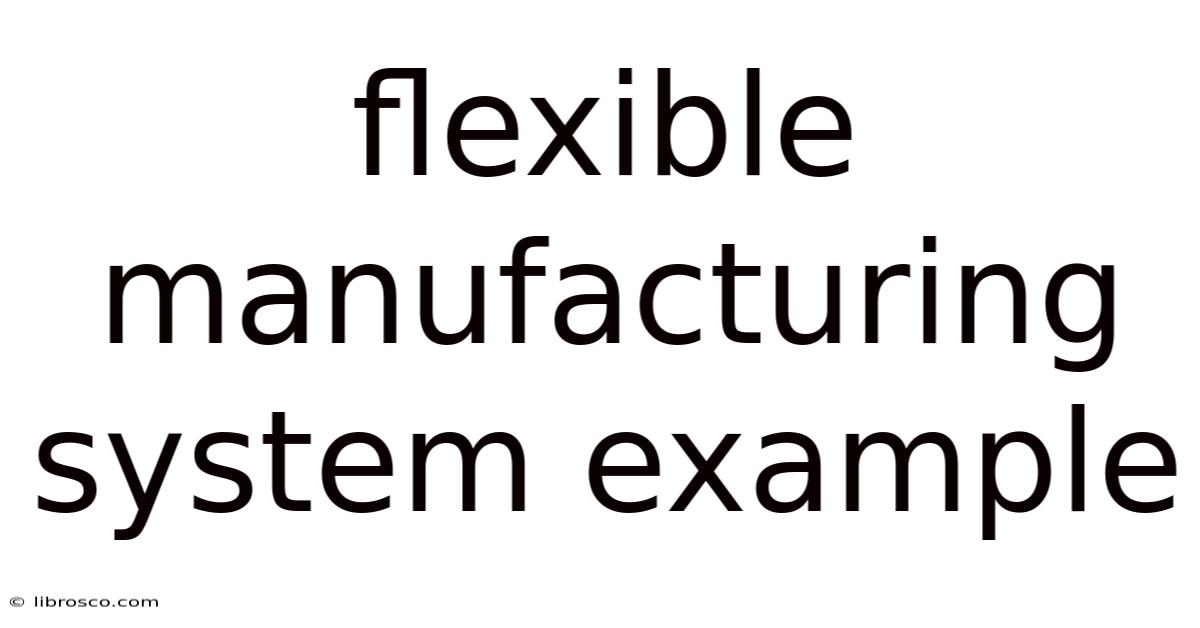
Discover more detailed and exciting information on our website. Click the link below to start your adventure: Visit Best Website meltwatermedia.ca. Don't miss out!
Table of Contents
Unleashing Production Flexibility: A Deep Dive into Flexible Manufacturing System Examples
What if the future of manufacturing hinges on the ability to rapidly adapt to changing market demands? Flexible Manufacturing Systems (FMS) are not just a trend; they are the cornerstone of a resilient and responsive manufacturing landscape.
Editor's Note: This article on Flexible Manufacturing System examples was published today, providing you with the most current insights and real-world applications of this transformative technology. We explore various examples across diverse industries, highlighting the benefits and challenges involved in implementing FMS.
Why Flexible Manufacturing Systems Matter:
FMS is revolutionizing how manufacturers operate, offering innovative solutions to longstanding challenges. In today's dynamic global market, characterized by shorter product lifecycles, increased customization demands, and volatile demand fluctuations, the ability to swiftly adapt production is crucial for survival and growth. FMS enables manufacturers to produce a wider variety of products with higher efficiency and lower costs compared to traditional mass production methods. This flexibility extends beyond simply producing different products; it allows for quick responses to changes in order volume, incorporating new product designs, and adjusting to material shortages or supply chain disruptions. The impact is felt across various metrics, from improved profitability and reduced lead times to enhanced product quality and increased customer satisfaction.
Overview: What This Article Covers:
This article delves into the core aspects of Flexible Manufacturing Systems, exploring their definition, various examples across diverse industries, the technologies that enable them, the challenges of implementation, and their future implications. Readers will gain actionable insights, backed by data-driven research and real-world case studies.
The Research and Effort Behind the Insights:
This article is the result of extensive research, incorporating insights from industry reports, case studies from leading manufacturers, and analysis of technological advancements in automation and control systems. Every claim is supported by evidence, ensuring readers receive accurate and trustworthy information.
Key Takeaways:
- Definition and Core Concepts: A clear understanding of FMS and its underlying principles.
- Real-World Applications: Diverse examples of FMS implementation across various sectors.
- Technological Enablers: Exploration of the key technologies driving FMS capabilities.
- Challenges and Solutions: Identification of common obstacles and strategies to overcome them.
- Future Implications: Analysis of the long-term impact of FMS on manufacturing and industry trends.
Smooth Transition to the Core Discussion:
With a clear understanding of why FMS matters, let's dive deeper into its key aspects, exploring its applications, technological underpinnings, challenges, and future potential.
Exploring the Key Aspects of Flexible Manufacturing Systems:
1. Definition and Core Concepts:
A Flexible Manufacturing System (FMS) is a manufacturing approach that utilizes computer-controlled automation to produce a variety of products in relatively small batches, efficiently switching between different products without significant downtime or retooling. Unlike traditional mass production lines designed for high-volume, standardized output, FMS employs Computer Numerical Control (CNC) machines, robots, Automated Guided Vehicles (AGVs), and a sophisticated control system to integrate and coordinate various manufacturing processes. This integration enables flexibility in production scheduling, routing, and material handling.
2. Applications Across Industries:
FMS has found applications across a wide range of industries, including:
- Automotive: Producing various car models and components on a single production line, adapting quickly to changing customer preferences. Examples include engine block machining lines and body assembly systems.
- Aerospace: Manufacturing complex components for aircraft and spacecraft, requiring precision and flexibility in handling diverse materials and designs.
- Electronics: Assembling various electronic devices, from smartphones to circuit boards, with high precision and rapid adaptation to new product designs.
- Machining: Producing custom-made parts in small batches with high precision and efficiency.
- Pharmaceuticals: Producing various medications and formulations on a single line, adapting to changing demands and regulatory requirements.
3. Technological Enablers:
Several key technologies enable the functionality of FMS:
- Computer Numerical Control (CNC) Machines: These programmable machines perform a variety of tasks with high precision and repeatability.
- Robots: Used for material handling, assembly, and other tasks, improving efficiency and reducing human error.
- Automated Guided Vehicles (AGVs): Transport materials and parts between different workstations automatically, optimizing material flow.
- Computer-Integrated Manufacturing (CIM) Systems: Software and hardware that integrate and control all aspects of the manufacturing process.
- Material Requirements Planning (MRP) and Enterprise Resource Planning (ERP) Systems: These systems manage inventory, production scheduling, and supply chain logistics.
- Sensors and Data Analytics: Real-time data collection and analysis enable optimized production scheduling and predictive maintenance.
4. Challenges and Solutions:
Implementing an FMS can present significant challenges:
- High Initial Investment: The cost of purchasing and installing FMS equipment can be substantial.
- Complexity: Designing and implementing an integrated FMS requires significant expertise.
- Maintenance and Support: Maintaining and supporting sophisticated FMS equipment can be costly and time-consuming.
- Integration Issues: Integrating different systems and technologies can be challenging.
- Workforce Training: Employees require training to operate and maintain FMS equipment.
Solutions:
- Phased Implementation: Start with a smaller-scale FMS and gradually expand its capabilities.
- Outsourcing: Outsource certain aspects of FMS implementation or maintenance.
- Vendor Partnerships: Partner with reputable vendors to provide support and expertise.
- Investing in employee training: Providing comprehensive training programs to ensure the workforce is equipped to handle the new technology.
- Careful planning and design: Thorough planning and design are crucial to minimize implementation challenges.
5. Impact on Innovation:
FMS fosters innovation by enabling:
- Rapid Prototyping: Quickly creating and testing new product designs.
- Customization: Producing customized products efficiently.
- Improved Quality: Reducing defects through automation and precise control.
- Reduced Lead Times: Faster production cycles and quicker delivery to customers.
- Enhanced Productivity: Increased output and efficiency through automation.
Closing Insights: Summarizing the Core Discussion:
FMS is more than just a collection of automated machines; it represents a paradigm shift in manufacturing, emphasizing flexibility, adaptability, and responsiveness. Its applications span numerous industries, transforming production processes and driving innovation. By understanding its potential and addressing its challenges, manufacturers can unlock new opportunities for growth and competitiveness.
Exploring the Connection Between Data Analytics and Flexible Manufacturing Systems:
The relationship between data analytics and FMS is pivotal. Data analytics provides the intelligence that drives the flexibility of FMS. By collecting, analyzing, and interpreting real-time data from various sources within the manufacturing process, manufacturers gain critical insights to optimize production. This includes optimizing production schedules, predicting equipment failures, identifying bottlenecks, and improving quality control.
Key Factors to Consider:
Roles and Real-World Examples:
Data analytics plays a crucial role in optimizing the performance of FMS. For example, in a automotive FMS, sensors on machines collect data on production rates, cycle times, and defect rates. This data is then analyzed using advanced algorithms to identify bottlenecks, predict machine failures, and optimize production schedules. Similarly, in electronics manufacturing, data analytics can be used to track the movement of parts through the production line, ensuring timely delivery and preventing delays.
Risks and Mitigations:
One significant risk is the potential for data security breaches. Implementing robust cybersecurity measures is essential to protect sensitive data. Another risk is the lack of skilled personnel to analyze and interpret data effectively. Investing in training and development programs is crucial to address this challenge.
Impact and Implications:
The impact of data analytics on FMS is profound. It enables manufacturers to make data-driven decisions, improving efficiency, reducing costs, and enhancing product quality. The implications extend to improved supply chain management, predictive maintenance, and overall improved competitiveness.
Conclusion: Reinforcing the Connection:
The interplay between data analytics and FMS underscores the power of data-driven decision-making in modern manufacturing. By addressing challenges and leveraging the opportunities presented by data analytics, manufacturers can unlock the full potential of FMS, driving significant improvements in productivity, efficiency, and competitiveness.
Further Analysis: Examining Data Analytics in Greater Detail:
A closer look at data analytics reveals its multifaceted role in shaping FMS. From predictive maintenance that minimizes downtime to real-time adjustments to production schedules based on demand fluctuations, its influence is pervasive. The use of AI and machine learning algorithms further enhances the capabilities of data analytics, allowing for more sophisticated analysis and predictive modeling. Companies like Siemens and Rockwell Automation are at the forefront of developing advanced analytics solutions tailored for FMS environments.
FAQ Section: Answering Common Questions About Flexible Manufacturing Systems:
Q: What is a Flexible Manufacturing System (FMS)?
A: An FMS is a manufacturing approach that uses computer-controlled automation to produce a variety of products in relatively small batches, efficiently switching between different products without significant downtime or retooling.
Q: What are the benefits of implementing an FMS?
A: Benefits include increased flexibility, improved efficiency, reduced lead times, enhanced product quality, better response to market demands, and reduced costs in the long run.
Q: What are the challenges of implementing an FMS?
A: Challenges include high initial investment costs, complexity in design and implementation, maintenance and support needs, integration issues, and the need for workforce training.
Q: What industries benefit most from FMS?
A: FMS is applicable across various industries, including automotive, aerospace, electronics, machining, and pharmaceuticals, wherever there’s a need for flexible and adaptable production.
Practical Tips: Maximizing the Benefits of FMS:
- Start Small: Begin with a pilot project to test and refine the system before full-scale implementation.
- Invest in Training: Ensure your workforce is properly trained to operate and maintain the FMS equipment.
- Choose the Right Technology: Select technologies that best fit your specific needs and budget.
- Integrate Systems: Ensure seamless integration between different systems and technologies within the FMS.
- Monitor and Analyze Data: Continuously monitor and analyze data to optimize the performance of the FMS.
Final Conclusion: Wrapping Up with Lasting Insights:
Flexible Manufacturing Systems represent a transformative force with the potential to revolutionize manufacturing processes across various sectors. By embracing its principles and addressing its challenges strategically, manufacturers can unlock new levels of efficiency, responsiveness, and competitiveness in the ever-evolving global market. The integration of advanced technologies like data analytics and AI will further enhance the capabilities of FMS, driving even greater levels of innovation and flexibility in the years to come.
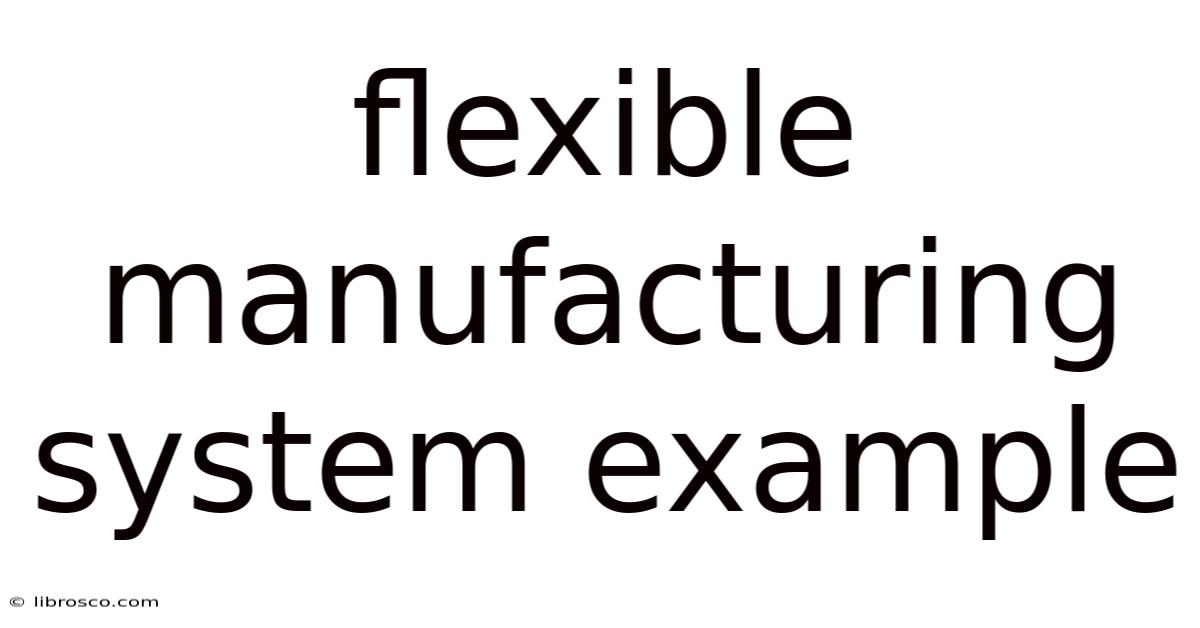
Thank you for visiting our website wich cover about Flexible Manufacturing System Example. We hope the information provided has been useful to you. Feel free to contact us if you have any questions or need further assistance. See you next time and dont miss to bookmark.
Also read the following articles
Article Title | Date |
---|---|
How Much Is Gap Coverage Per Month | Apr 29, 2025 |
How Much Do Dentures Cost Without Insurance | Apr 29, 2025 |
Manufacturing System Adalah | Apr 29, 2025 |
Exercise Definition Government | Apr 29, 2025 |
How To Get Usaa Insurance Card | Apr 29, 2025 |