Define Offset In Process Control
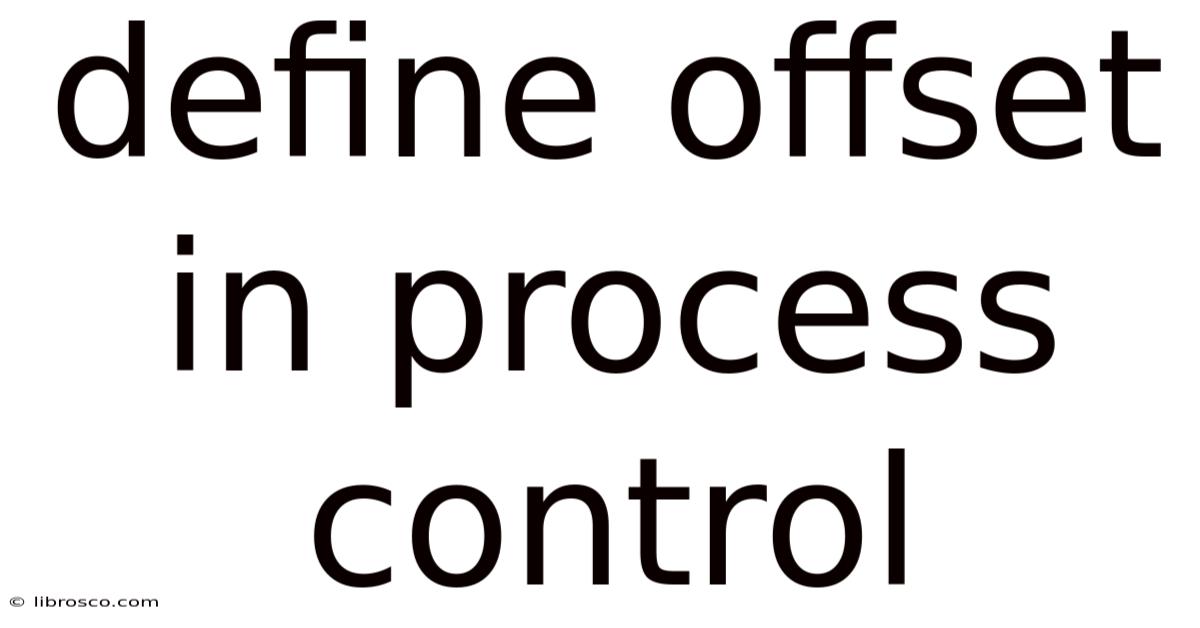
Discover more detailed and exciting information on our website. Click the link below to start your adventure: Visit Best Website meltwatermedia.ca. Don't miss out!
Table of Contents
Defining Offset in Process Control: Understanding and Minimizing Persistent Deviations
What if consistent deviations from setpoints hampered your process efficiency and product quality? Understanding and mitigating offset in process control is crucial for optimal performance and profitability.
Editor’s Note: This article on offset in process control was published today, providing readers with up-to-date insights and practical strategies for improving process control systems. This in-depth exploration covers the definition, causes, consequences, and mitigation techniques relevant to various industrial processes.
Why Offset Matters: Relevance, Practical Applications, and Industry Significance
Offset, in the context of process control, refers to the persistent difference between a measured process variable and its desired setpoint. This steady-state error isn't a transient fluctuation; it's a continuous deviation that remains even after the control system has supposedly reached equilibrium. This seemingly small discrepancy can have significant implications across diverse industries, from manufacturing and chemical processing to power generation and environmental monitoring. Offset leads to suboptimal product quality, increased energy consumption, material waste, and ultimately, reduced profitability. Understanding and addressing offset is paramount for maintaining process stability, enhancing efficiency, and ensuring product consistency. The impact extends beyond simple economic considerations; in safety-critical processes, consistent offset can pose significant risks.
Overview: What This Article Covers
This comprehensive article explores the multifaceted nature of offset in process control. We'll delve into its fundamental definition, explore the common causes behind its occurrence, analyze its detrimental consequences, and provide practical strategies for its effective mitigation. We’ll examine different control strategies, their strengths and weaknesses regarding offset, and how process parameters influence the magnitude of offset. Finally, we’ll address common questions and offer actionable tips for optimizing process control systems.
The Research and Effort Behind the Insights
This article is the result of extensive research, drawing upon established control theory principles, industry best practices, and numerous case studies from diverse sectors. The information presented is supported by reliable data sources, academic publications, and practical experience in process control engineering.
Key Takeaways:
- Definition and Core Concepts: A clear understanding of offset and its distinction from other process variations.
- Causes of Offset: Identification of common factors contributing to persistent deviations.
- Consequences of Offset: Analysis of the negative impacts on process efficiency, product quality, and safety.
- Mitigation Strategies: Practical techniques and control algorithms for minimizing or eliminating offset.
- Advanced Control Techniques: Exploration of more sophisticated methods for offset reduction.
Smooth Transition to the Core Discussion
Having established the importance of understanding offset, let's now delve into the specifics, analyzing its causes, impact, and effective mitigation strategies.
Exploring the Key Aspects of Offset in Process Control
1. Definition and Core Concepts:
Offset, also known as steady-state error, represents the persistent difference between the actual value of a controlled variable and its desired setpoint after the system has settled. This is in contrast to transient errors, which are temporary deviations that eventually diminish. Offset indicates an imbalance in the control loop, preventing the system from reaching the desired target accurately. The magnitude of offset is typically expressed as a numerical difference or percentage deviation from the setpoint.
2. Causes of Offset:
Several factors can contribute to the presence of offset in a process control system. These include:
- Non-linearity: Many industrial processes exhibit non-linear behavior, meaning that the relationship between the manipulated variable (e.g., valve position) and the controlled variable (e.g., temperature) isn't consistently proportional. This non-linearity can lead to persistent deviations.
- Process Disturbances: Unpredictable variations in feedstock composition, ambient conditions, or other external factors can introduce persistent offsets. These disturbances may overwhelm the control system's ability to maintain the setpoint accurately.
- Integrator Windup: This phenomenon occurs in controllers with integral action when the manipulated variable reaches its limits (e.g., valve fully open or closed). The integral term continues to accumulate error, even when the system is saturated, leading to large offsets upon the removal of the saturation.
- Improper Controller Tuning: Incorrectly tuned proportional-integral-derivative (PID) controllers can result in significant offset. If the integral gain is too low, the controller may not be able to effectively eliminate the error, while an excessively high integral gain can lead to instability and oscillations.
- Measurement Errors: Inaccurate or noisy measurements of the controlled variable can lead to incorrect controller actions, resulting in persistent offsets. Sensor drift or calibration issues are common contributors.
- Dead Time: The delay between a controller action and its effect on the process variable (dead time) can hinder the controller's ability to accurately compensate for disturbances and maintain the setpoint, leading to offset.
- Model-Plant Mismatch: If the mathematical model used to design and tune the controller doesn't accurately reflect the actual process dynamics, offset is likely to occur.
3. Consequences of Offset:
The presence of offset can have several detrimental effects:
- Reduced Product Quality: Persistent deviations from the setpoint can lead to inconsistent product quality, potentially resulting in defects, waste, and increased rejection rates.
- Increased Energy Consumption: Offset often requires the control system to continuously compensate for the deviation, leading to increased energy consumption and operational costs.
- Equipment Damage: Persistent deviations can stress equipment components, potentially leading to premature wear and tear, requiring costly repairs or replacements.
- Safety Concerns: In safety-critical processes, consistent offsets can represent a significant safety hazard, potentially leading to accidents or incidents.
- Economic Losses: The combined effect of reduced quality, increased energy consumption, equipment damage, and potential safety issues translates to substantial economic losses for the company.
4. Mitigation Strategies:
Several strategies can be implemented to minimize or eliminate offset:
- Proper Controller Tuning: Careful tuning of the PID controller parameters is essential. Techniques like Ziegler-Nichols method or advanced auto-tuning algorithms can help optimize controller performance.
- Feedforward Control: Implementing a feedforward control loop can compensate for predictable disturbances before they affect the controlled variable, minimizing the need for corrective actions from the feedback loop and reducing offset.
- Offset Compensation: Some controllers incorporate explicit offset compensation mechanisms, directly adjusting the controller output to correct for the persistent deviation.
- Improved Measurement Systems: Using high-quality, calibrated sensors and minimizing measurement noise are crucial steps in achieving accurate control and reducing offset.
- Process Linearization: Employing techniques to linearize the process response can improve the effectiveness of linear control algorithms and reduce offset.
- Advanced Control Strategies: More sophisticated control strategies such as model predictive control (MPC) or internal model control (IMC) can effectively handle non-linearities and disturbances, significantly minimizing offset.
- Cascade Control: Employing a cascade control structure, where a secondary loop controls a key intermediate variable that impacts the primary controlled variable, can often improve control performance and minimize offset.
5. Impact on Innovation:
The ongoing research into improved control algorithms, advanced sensor technologies, and sophisticated process modeling techniques is directly aimed at minimizing or eliminating offset. This pursuit of improved process control contributes to enhanced manufacturing efficiency, product quality, and sustainability across various industrial sectors.
Closing Insights: Summarizing the Core Discussion
Offset is a critical consideration in process control, representing a persistent deviation from the desired setpoint that can have severe consequences. Through a comprehensive understanding of its causes and effective application of mitigation strategies, industries can achieve improved process stability, enhanced product quality, and significant economic benefits.
Exploring the Connection Between Process Non-linearity and Offset
Process non-linearity is a significant contributor to offset. It arises when the relationship between the manipulated variable and the controlled variable isn't consistently proportional. For instance, in a chemical reactor, the reaction rate might not be linearly proportional to temperature changes; a small temperature increase might initially accelerate the reaction significantly but then show diminishing returns at higher temperatures.
Key Factors to Consider:
- Roles and Real-World Examples: Consider a heat exchanger controlling fluid temperature. A non-linear heat transfer coefficient can create offset, as the controller's linear model may inaccurately represent the actual heat transfer at different temperatures.
- Risks and Mitigations: Non-linearity can lead to substantial offset, particularly if the controller is tuned based on a simplified linear model. Mitigation strategies include using advanced control algorithms that can handle non-linearity, such as MPC, or employing process linearization techniques.
- Impact and Implications: Ignoring non-linearity can result in persistent offset, affecting product quality, energy efficiency, and overall profitability. Understanding and addressing non-linearity is crucial for achieving optimal process control.
Conclusion: Reinforcing the Connection
The connection between process non-linearity and offset is undeniably strong. Effective control system design must explicitly account for non-linear behavior to minimize the negative impacts of offset and achieve superior process performance.
Further Analysis: Examining Process Disturbances in Greater Detail
Process disturbances are unpredictable variations in input variables or environmental conditions that affect the controlled process. These disturbances can be caused by fluctuations in feedstock composition, ambient temperature changes, variations in pressure, or other external factors.
FAQ Section: Answering Common Questions About Offset
- What is offset and why does it matter? Offset is the persistent difference between the actual and desired value of a process variable. It leads to inconsistent product quality, increased energy consumption, and potential safety hazards.
- How can I identify offset in my process? Monitor the process variable over time and look for a consistent deviation from the setpoint, even after the system appears to have settled.
- What are the most common causes of offset? Non-linear process behavior, improper controller tuning, process disturbances, measurement errors, and dead time are frequent contributors.
- What are some effective strategies to reduce offset? Proper controller tuning, feedforward control, offset compensation, improved measurement systems, and advanced control strategies can all help minimize or eliminate offset.
Practical Tips: Maximizing the Benefits of Effective Offset Mitigation
- Regularly monitor your process variables: Continuous monitoring allows for early detection of offset and timely intervention.
- Perform thorough controller tuning: Use appropriate tuning methods to optimize controller performance and minimize offset.
- Implement robust measurement systems: High-quality sensors and effective noise reduction techniques ensure accurate measurements.
- Consider advanced control strategies: Explore the use of MPC or other advanced techniques for handling non-linearities and disturbances.
- Analyze process data for patterns: Identifying recurring disturbances or non-linear behaviors can inform targeted mitigation strategies.
Final Conclusion: Wrapping Up with Lasting Insights
Offset in process control is a pervasive challenge that can significantly impact industrial operations. By understanding its causes, consequences, and the available mitigation strategies, engineers and operators can improve process efficiency, product quality, and overall profitability. Continuous monitoring, careful controller tuning, and strategic implementation of advanced control technologies are key to achieving superior process control and minimizing the impact of offset. The pursuit of minimizing offset is an ongoing challenge driving innovation and improvement within the field of process control.
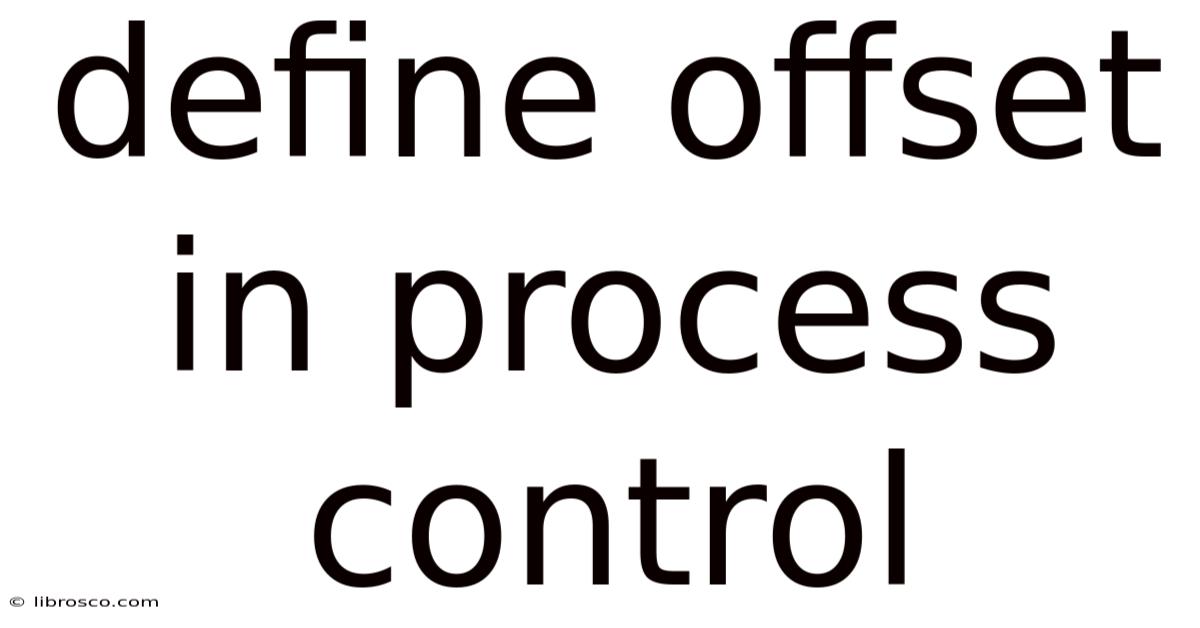
Thank you for visiting our website wich cover about Define Offset In Process Control. We hope the information provided has been useful to you. Feel free to contact us if you have any questions or need further assistance. See you next time and dont miss to bookmark.
Also read the following articles
Article Title | Date |
---|---|
Convertible Life Assurance | Apr 21, 2025 |
Life Insurance Age Limit Uk | Apr 21, 2025 |
Define Order Of Differential Equation | Apr 21, 2025 |
Can I Cancel My Geico Insurance On The App | Apr 21, 2025 |
Hdfc Billing Cycle Credit Card | Apr 21, 2025 |