Define Offset In Control System
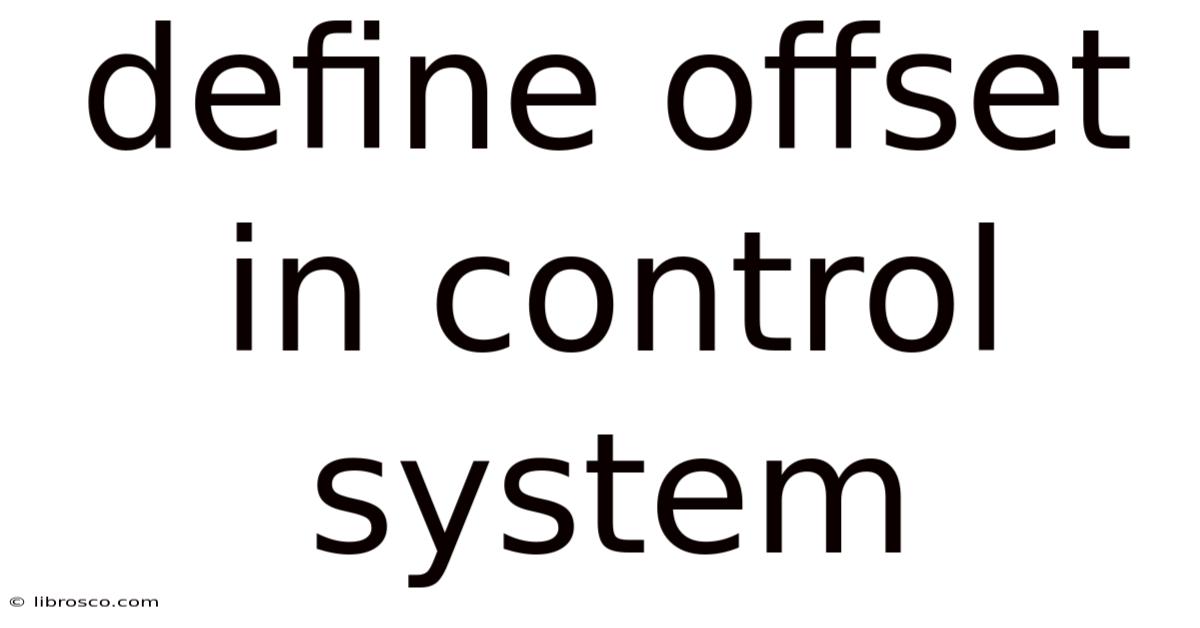
Discover more detailed and exciting information on our website. Click the link below to start your adventure: Visit Best Website meltwatermedia.ca. Don't miss out!
Table of Contents
Defining Offset in Control Systems: Understanding, Minimizing, and Eliminating Persistent Errors
What if the precision of your control system hinges on understanding and eliminating offset? Offset, a persistent deviation from the desired setpoint, is a critical challenge in control system design and implementation that significantly impacts performance and accuracy.
Editor’s Note: This article on offset in control systems was published today, providing readers with the latest insights and best practices for understanding and mitigating this common control problem.
Why Offset Matters: Relevance, Practical Applications, and Industry Significance
Offset, also known as steady-state error, represents the difference between the desired output (setpoint) and the actual output of a control system after the system has settled. This persistent deviation significantly impacts the performance and accuracy of various systems across numerous industries. In manufacturing, offset can lead to inconsistent product quality, wasted materials, and production delays. In process control, it can affect efficiency, safety, and overall productivity. In robotics and automation, even small offsets can accumulate, leading to significant errors over time. The implications extend to virtually any application where precise control is critical, including HVAC systems, automotive cruise control, and even spacecraft navigation. Understanding and mitigating offset is crucial for achieving optimal system performance. This includes optimizing energy consumption, improving safety, and enhancing overall product quality.
Overview: What This Article Covers
This article provides a comprehensive exploration of offset in control systems. We will delve into the underlying causes of offset, explore different types of control systems and their susceptibility to offset, discuss various techniques for offset reduction and elimination, and provide real-world examples to illustrate the practical implications. Readers will gain a solid understanding of how to identify, analyze, and address offset in their own control system designs.
The Research and Effort Behind the Insights
This article draws upon extensive research, including textbooks on control systems engineering, peer-reviewed journal articles, and industry best practices. The information presented is supported by established control theory and real-world application examples, ensuring accuracy and credibility. The analysis incorporates various control system configurations and their unique challenges related to offset minimization.
Key Takeaways:
- Definition and Core Concepts: A thorough explanation of offset, its causes, and its impact on control system performance.
- Types of Control Systems and Offset: An analysis of how different control architectures (e.g., proportional, integral, derivative, PID) handle offset.
- Offset Reduction Techniques: A detailed overview of methods for minimizing or eliminating offset, including integral action, feedforward control, and others.
- Case Studies and Real-World Examples: Practical illustrations of offset problems and their solutions across diverse industries.
- Advanced Techniques: A brief exploration of more sophisticated methods like model predictive control (MPC) for handling complex offset scenarios.
Smooth Transition to the Core Discussion:
Having established the significance of offset in control systems, let's now dive into a detailed examination of its causes, consequences, and mitigation strategies.
Exploring the Key Aspects of Offset in Control Systems
1. Definition and Core Concepts:
Offset is the persistent difference between the desired value (setpoint) and the actual value of a controlled variable after the system has reached steady state. It's a static error that remains even when the system is seemingly stable. This error stems from the inability of certain control systems to perfectly match the output to the setpoint due to inherent limitations in the control algorithm or the system's dynamics.
2. Types of Control Systems and Offset:
-
Proportional (P) Control: P-control systems only react to the difference between the setpoint and the actual output (error). They often suffer from significant offset because they lack the capability to eliminate the steady-state error. The output is proportional to the error, but if there's a constant disturbance, a constant error will persist.
-
Integral (I) Control: I-control systems accumulate the error over time. This accumulated error is used to drive the control action. The integral term ensures that the steady-state error is eventually eliminated. However, I-control can be slow to respond initially and may lead to overshoot.
-
Derivative (D) Control: D-control systems react to the rate of change of the error. This anticipates future errors and improves the system's transient response, reducing overshoot and oscillations. It doesn't directly address offset.
-
Proportional-Integral (PI) Control: PI control combines the advantages of both P and I controllers. The proportional term provides quick response, while the integral term eliminates steady-state error. This is a very common and effective control strategy.
-
Proportional-Integral-Derivative (PID) Control: PID control incorporates all three terms (P, I, D) for optimal control performance. It provides a fast response, reduces overshoot, and eliminates steady-state error. PID controllers are widely used due to their versatility and effectiveness in many applications.
3. Offset Reduction Techniques:
-
Integral Action: The most common method to eliminate offset is through integral action. The integral term continuously sums the error, driving the output towards the setpoint until the error is zero.
-
Feedforward Control: Feedforward control anticipates disturbances and compensates for them before they affect the output. This is particularly effective when the disturbances are predictable.
-
Offset Compensation: This involves adding a constant term to the control signal to compensate for the known offset. This approach relies on accurate system modeling and knowledge of the steady-state error.
-
Tuning of Controller Gains: Proper tuning of the proportional, integral, and derivative gains in a PID controller is critical for minimizing offset and ensuring stable system operation. Improper tuning can lead to excessive oscillations or persistent error.
-
System Calibration and Identification: Accurate calibration of sensors and actuators and precise system identification are essential for reducing errors caused by inaccurate measurements or model uncertainties.
4. Case Studies and Real-World Examples:
-
Temperature Control: In a heating system, offset could lead to inconsistent room temperature. A well-tuned PID controller with integral action can maintain the desired temperature despite external disturbances (like opening a window).
-
Process Control in Chemical Plants: Maintaining precise concentrations of chemicals is crucial. Offset in the control system can result in product quality issues, safety hazards, or waste.
-
Robotics and Automation: In robotic arms, even small offsets can accumulate, leading to significant positioning errors over time. Precise control and calibration are crucial to minimize these errors.
5. Advanced Techniques:
- Model Predictive Control (MPC): MPC utilizes a system model to predict future behavior and optimize control actions accordingly. This approach can effectively handle complex systems and disturbances, minimizing offset. It's particularly suitable for multivariable systems with constraints.
Closing Insights: Summarizing the Core Discussion
Offset, a persistent deviation from the desired setpoint, is a significant challenge in many control systems. While some simple controllers struggle with offset, others, notably those incorporating integral action, can effectively eliminate it. The choice of controller, the tuning of its parameters, and techniques like feedforward control are all critical in managing and minimizing this error. Understanding and mitigating offset are paramount for achieving optimal system performance across various applications.
Exploring the Connection Between Disturbances and Offset
Disturbances are external factors affecting the system's output, causing deviations from the setpoint. They play a critical role in generating offset in control systems.
Key Factors to Consider:
-
Roles and Real-World Examples: Disturbances can range from changes in ambient temperature (affecting a heating system) to variations in raw material composition (impacting a chemical process). These disturbances create errors that a purely proportional controller cannot fully correct, leading to offset.
-
Risks and Mitigations: Ignoring disturbances can result in significant offset, impacting product quality, safety, and efficiency. Mitigation strategies include feedforward control (anticipating disturbances) and robust control design (making the system less sensitive to disturbances).
-
Impact and Implications: Persistent offset due to disturbances can lead to inefficiencies, increased energy consumption, and potentially dangerous operating conditions.
Conclusion: Reinforcing the Connection
The relationship between disturbances and offset is fundamental in control systems. Understanding the nature and impact of disturbances is essential for designing effective control strategies that minimize or eliminate offset.
Further Analysis: Examining Disturbances in Greater Detail
Disturbances can be classified as deterministic (predictable) or stochastic (random). Deterministic disturbances can be compensated for using feedforward control, while stochastic disturbances often require robust control techniques or feedback mechanisms to minimize their impact on the system's output.
FAQ Section: Answering Common Questions About Offset in Control Systems
-
Q: What is the most common cause of offset?
- A: The most common cause is the lack of integral action in the control system. Proportional-only controllers will generally exhibit significant offset in the presence of disturbances.
-
Q: How can I reduce offset in my PID controller?
- A: Carefully tune the integral gain (Ki). A too-small Ki will result in slow offset correction, while a too-large Ki can lead to oscillations and instability.
-
Q: What are the consequences of ignoring offset?
- A: Ignoring offset can result in inconsistent output, reduced product quality, increased energy consumption, and potentially unsafe operating conditions.
-
Q: What is the difference between transient and steady-state error?
- A: Transient error refers to the error during the system's response to a change in the setpoint or a disturbance. Steady-state error, or offset, is the persistent error that remains after the transient response has settled.
Practical Tips: Maximizing the Benefits of Offset Reduction
-
Accurate System Modeling: Create a precise model of your system to better understand its dynamics and how disturbances affect it.
-
Proper Controller Selection: Choose a controller appropriate for your system's requirements. For applications requiring zero steady-state error, an integral term is essential.
-
Careful Controller Tuning: Systematically tune the controller gains to optimize its performance and minimize offset.
-
Disturbance Mitigation: Implement feedforward control or other techniques to reduce the impact of predictable disturbances.
-
Regular System Maintenance: Regular calibration and maintenance of sensors and actuators are crucial for maintaining accuracy and minimizing offset.
Final Conclusion: Wrapping Up with Lasting Insights
Offset is a critical factor to consider in control system design and implementation. Understanding its causes, consequences, and mitigation strategies is crucial for achieving optimal system performance. By employing appropriate control strategies and techniques, designers can minimize or eliminate offset, resulting in improved efficiency, accuracy, and overall system reliability. The careful selection and tuning of controllers, combined with a thorough understanding of system dynamics and disturbances, are essential steps in achieving precise and stable control.
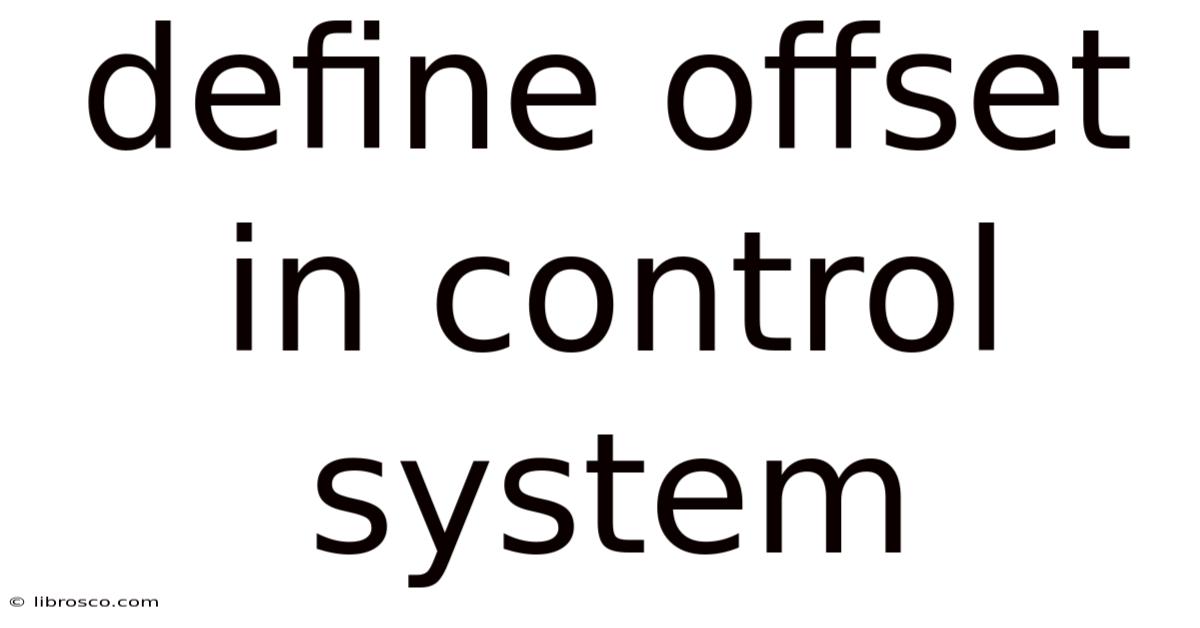
Thank you for visiting our website wich cover about Define Offset In Control System. We hope the information provided has been useful to you. Feel free to contact us if you have any questions or need further assistance. See you next time and dont miss to bookmark.
Also read the following articles
Article Title | Date |
---|---|
What Is Money Weighted Return | Apr 21, 2025 |
Obsolete Inventory Formula | Apr 21, 2025 |
When Does Insurable Interest Exist In A Life Insurance Contract | Apr 21, 2025 |
What Is Tax Basis Accounting | Apr 21, 2025 |
Define Order Of Reaction Class 12 Chemistry | Apr 21, 2025 |